Examine key elements like f
Step-by-Step Guide to Engine Maintenance
Proper upkeep of an engine ensures its longevity and smooth operation. By following a systematic approach, you can prevent common issues and extend the life of the equipment. Regular inspections, adjustments, and replacements are key aspects of maintaining an engine’s optimal performance.
Start by turning off the power source and allowing the engine to cool down completely. This reduces the risk of accidents and ensures a safer working environment. Check for visible wear or damage, including leaks, corrosion, or loose connections. Addressing these concerns early can prevent larger, costlier problems.
Next, clean or replace the air filter to ensure a steady airflow, as a blocked filter can reduce efficiency. Examine the fuel system, including hoses and connections, for any signs of wear or leaks. Replace faulty parts to maintain consistent fuel delivery.
Oil plays a vital role in lubrication, reducing friction and preventing overheating. Regularly check the oil level and change it according to the recommended intervals. Use quality oil that meets the specifications to enhance engine performance.
Inspect the spark plugs and ignition components. Clean or replace them if needed, as faulty ignition parts can lead to inefficient starts or misfiring. Finally, perform a routine test run to ensure all systems are functioning correctly. Listening for unusual sounds and observing performance indicators can help detect any underlying issues.
Replacing Faulty Parts in Generators
Identifying and replacing malfunctioning components is essential for ensuring reliable performance and prolonged operation of any power equipment. When certain parts begin to wear out or fail, immediate attention is required to prevent further complications. The process typically involves a thorough inspection, careful removal of defective elements, and precise installation of new ones.
Before starting any replacement procedure, it is crucial to disconnect the device from its power source to avoid accidents. Examine the unit carefully, checking for signs of corrosion, damaged wires, or broken connections. Using appropriate tools, remove the faulty elements one at a time, ensuring not to disturb other parts. Each new piece should be carefully aligned and secured to guarantee optimal functionality.
After installation, it is recommended to conduct a test run to confirm that the system operates smoothly and efficiently. Regular checks and timely part replacements can help maintain the system’s overall health and avoid unexpected disruptions in the future.
Tips for Extending Generator Lifespan
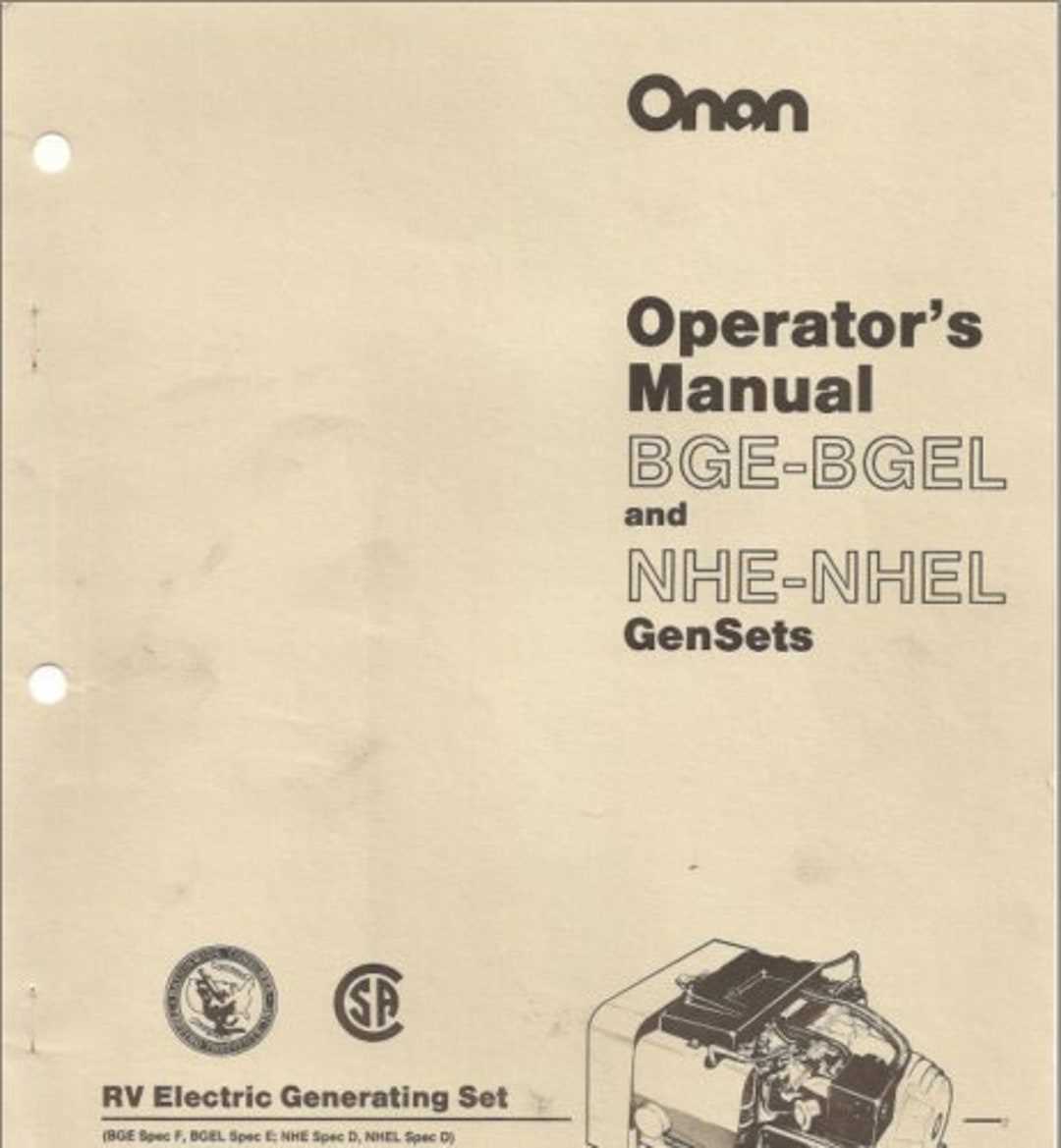
Maintaining the longevity of your power-producing equipment is essential for optimal performance and efficiency. By implementing a few simple practices, you can enhance its durability and reduce the likelihood of unexpected breakdowns. This section provides practical advice to ensure your device remains reliable for years to come.
Regular Maintenance
Consistent upkeep is crucial for preserving functionality. Routine inspections and servicing can prevent minor issues from escalating into significant problems. Consider scheduling checks every few months, focusing on the following areas:
Maintenance Task |
Frequency |
Oil Change |
Every 50 hours of use |
Air Filter Cleaning |
Every month |
Fuel System Check |
Every season |
Battery Maintenance |
Every three months |
Optimal Storage Conditions
Storing your equipment in a suitable environment is vital for its lifespan. Protect it from extreme temperatures, moisture, and debris. Ensure it is covered when not in use and consider a sheltered location to minimize exposure to the elements.
Understanding Generator Wiring Diagrams
Wiring diagrams serve as essential tools for comprehending the electrical connections within power-producing devices. They provide a visual representation of the components and their interrelations, allowing users to grasp the flow of electricity and troubleshoot potential issues effectively. By analyzing these diagrams, one can gain insights into the operational principles and safety measures necessary for optimal performance.
Components of Wiring Diagrams
A wiring diagram typically includes various elements such as symbols for switches, relays, and fuses, along with lines representing electrical connections. Familiarity with these symbols is crucial for interpreting the schematic accurately. Below is a table highlighting common symbols found in wiring diagrams:
Symbol |
Description |
⚫ |
Connection Point |
➔ |
Direction of Current Flow |
⏏ |
Switch |
⏚ |
Ground Connection |
Interpreting the Diagrams
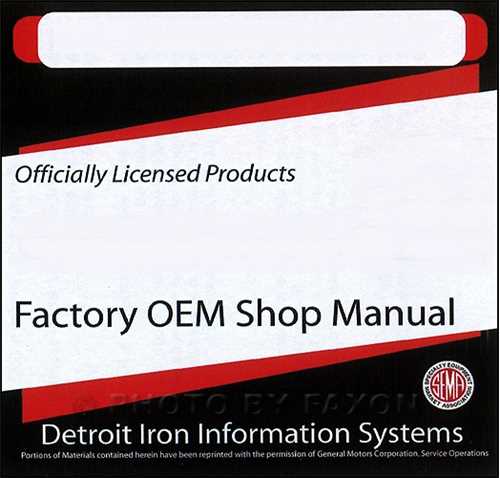
To effectively utilize wiring schematics, one must start by identifying the power source and tracing the connections to the various components. By following the paths indicated in the diagrams, users can determine how power is distributed throughout the system, aiding in the diagnosis of faults or inefficiencies. Understanding the layout and function of each component is vital for maintaining the reliability and safety of the equipment.
Cleaning and Lubrication Best Practices
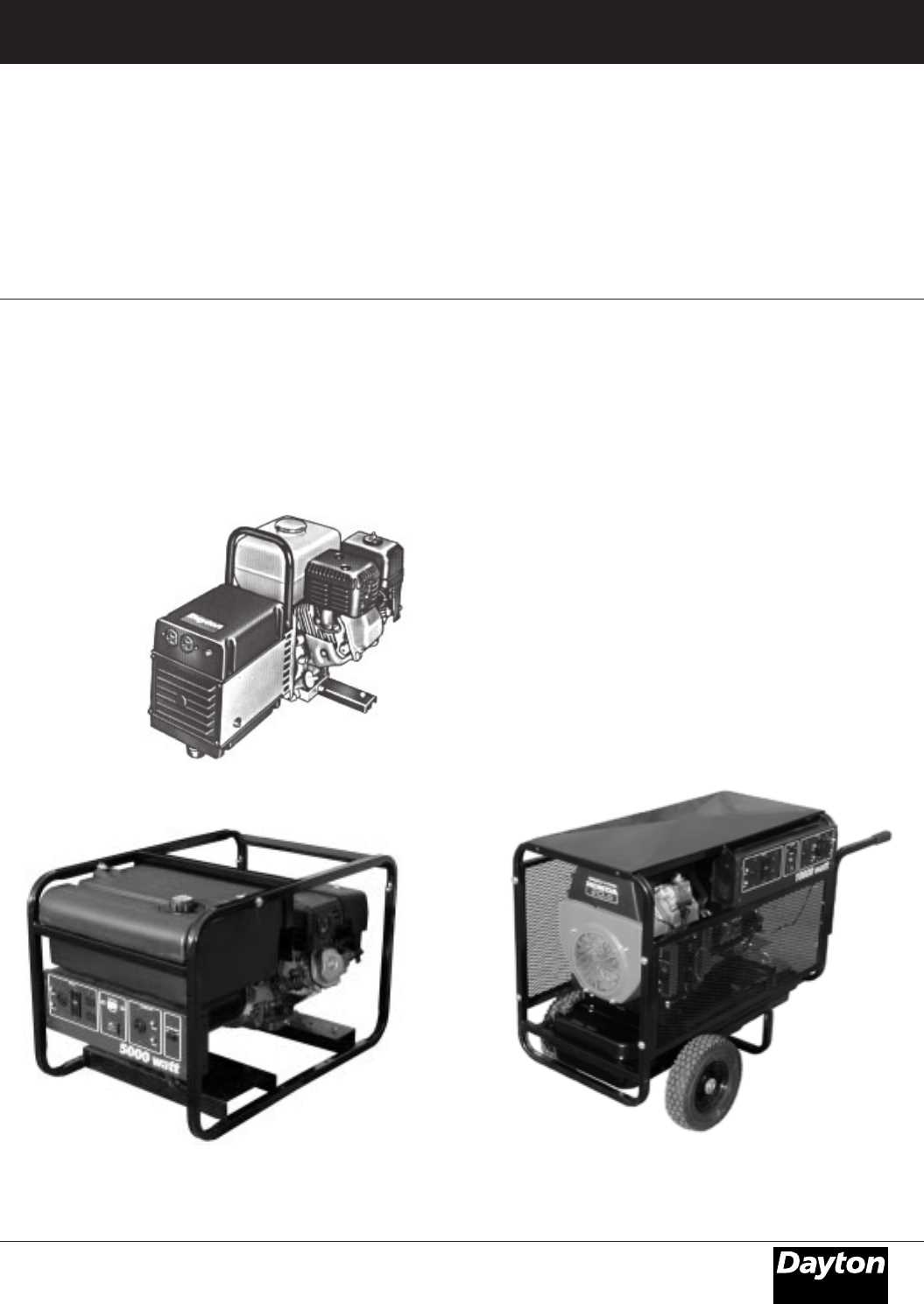
Maintaining optimal performance of machinery requires regular upkeep, particularly through effective cleaning and lubrication. These practices not only enhance efficiency but also prolong the lifespan of the equipment. Adopting a systematic approach ensures that all components operate smoothly, reducing the likelihood of wear and malfunction.
Essential Cleaning Techniques
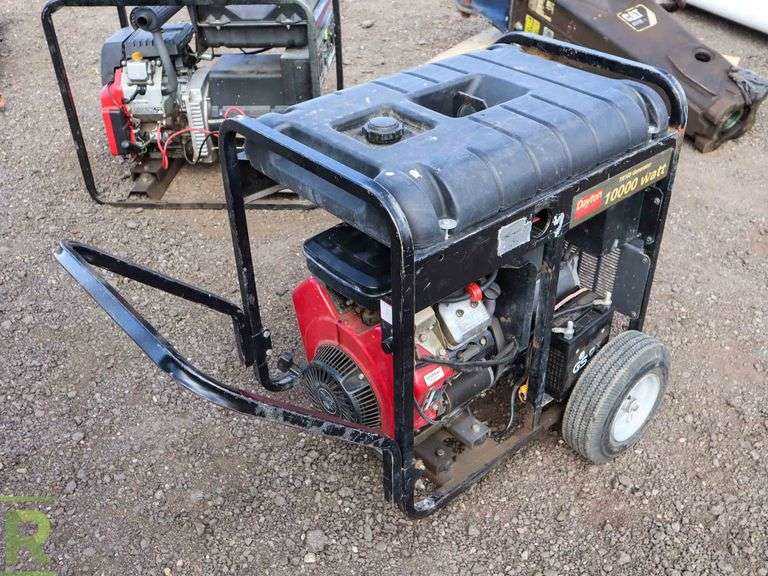
Regular cleaning is vital for removing dirt and debris that can hinder operation. Utilize the following methods to achieve effective results:
Method |
Description |
Dry Cleaning |
Use a soft brush or compressed air to eliminate dust and particles from surfaces. |
Wet Cleaning |
Employ mild detergents and cloths for surfaces requiring deeper cleaning. Ensure components are dried thoroughly afterward. |
Disassembly |
For thorough cleaning, consider disassembling accessible parts. Clean individually before reassembly. |
Optimal Lubrication Practices
Proper lubrication reduces friction, thereby enhancing the efficiency of moving parts. Follow these best practices for effective application:
Type of Lubricant |
Application Method |
Grease |
Apply to bearings and gears where longer-lasting lubrication is required. |
Oil |
Use for parts that require frequent application; ensure regular checks for oil levels. |
Synthetic Lubricants |
Consider for extreme temperatures or heavy loads; they often offer superior protection. |
Choosing Replacement Parts for Dayton Models
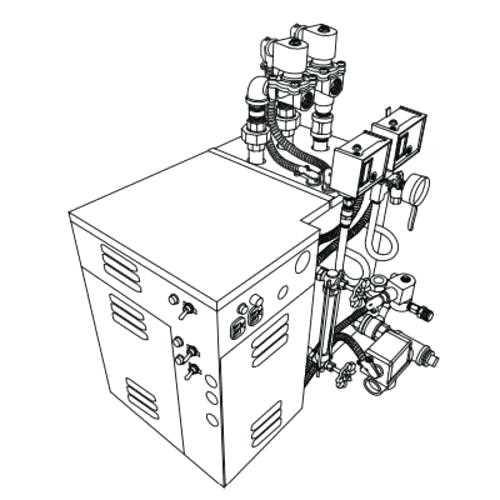
When maintaining or restoring your power-producing equipment, selecting the right components is crucial for optimal performance. Each unit is designed with specific functionalities, and using suitable substitutes ensures longevity and efficiency.
Begin by identifying the model number and specifications of your device. This information serves as a guide to find compatible elements. Consult manufacturer guidelines or trusted suppliers to verify that the parts meet necessary standards.
Additionally, consider quality over cost. Investing in durable components often results in better performance and reduces the frequency of replacements. Look for reputable brands that offer warranties, as this can be an indicator of reliability.
Research is key. Check customer reviews and feedback to gauge the performance of particular parts. Online forums and user groups can provide valuable insights from others who have faced similar challenges.
Ultimately, making informed decisions about replacements can significantly enhance the functionality of your machinery, ensuring it operates smoothly for years to come.
Preventive Maintenance for Reliable Performance
Ensuring consistent functionality of machinery requires proactive care and attention. Regular upkeep not only extends the lifespan of equipment but also enhances operational efficiency. Implementing a well-structured maintenance routine can significantly reduce the likelihood of unexpected breakdowns, leading to smoother and more reliable performance.
Key Aspects of Preventive Care
- Regular Inspections: Conducting systematic evaluations helps identify wear and tear before it becomes problematic.
- Lubrication: Keeping moving parts well-lubricated minimizes friction, thus preventing excessive wear.
- Cleaning: Removing debris and dirt from components ensures optimal operation and reduces overheating.
- Electrical Checks: Verifying connections and wiring integrity prevents electrical failures.
Maintenance Schedule Recommendations
- Perform a detailed inspection monthly.
- Schedule lubrication every three months.
- Clean all accessible areas quarterly.
- Conduct electrical system evaluations bi-annually.
By adhering to these guidelines, one can achieve enhanced reliability and efficiency in performance, ultimately resulting in better productivity and fewer interruptions.
|