Inspection |
Examine gears, bearings, and seals for signs of wear, cracks, or deformation. Replace any components that show significant wear or damage to prevent future breakdowns. |
Cooling System Service Tips
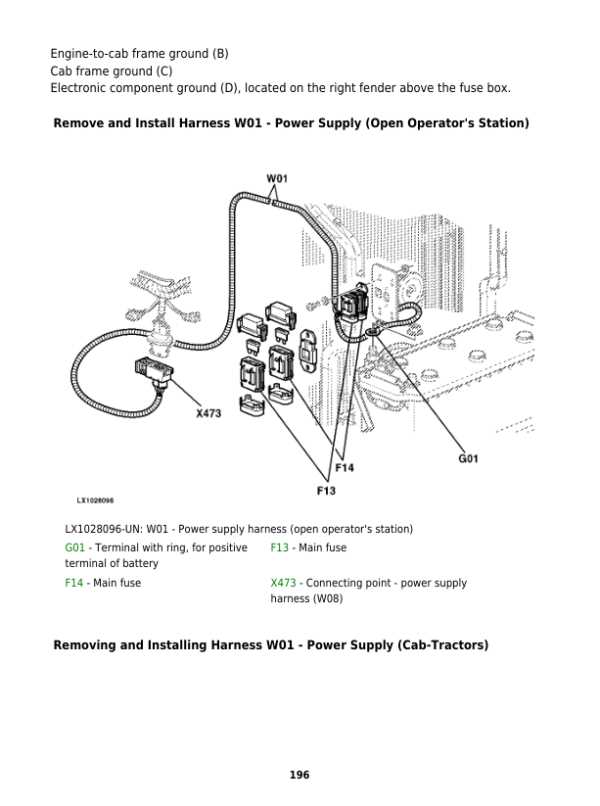
Proper maintenance of the cooling system is essential for ensuring optimal performance and longevity of agricultural machinery. Regular checks and servicing can prevent overheating and other issues that may lead to costly repairs and downtime. Here are some practical tips to help maintain the efficiency of the cooling system.
First, regularly inspect coolant levels and top up as necessary. This should be done when the engine is cool to avoid injury. Use the recommended coolant type to ensure compatibility and effectiveness. Additionally, monitor for any signs of leaks, which can indicate potential problems within the system.
Next, ensure that the radiator and cooling fins are clean and free from debris. Blockages can impede airflow, reducing the cooling efficiency. A gentle cleaning with compressed air or water can help maintain proper function. Always refer to the manufacturer’s guidelines for specific cleaning techniques.
It is also advisable to check the thermostat and water pump for any signs of wear or malfunction. These components play a crucial role in regulating engine temperature. If you notice fluctuations in temperature or unusual noises from the water pump, consider having these parts inspected by a professional.
Lastly, keep an eye on hoses and clamps for signs of wear or damage. Replacing any cracked or worn hoses can prevent leaks and ensure a reliable cooling system. Regular service intervals are recommended to keep the system functioning smoothly and efficiently.
Fuel System Repair Procedures
The fuel system is a vital component of any agricultural machine, ensuring the proper delivery of fuel to the engine for optimal performance. This section outlines essential techniques and steps for addressing common issues within this system, facilitating effective maintenance and enhancing machine reliability.
Inspection and Diagnosis: Begin by conducting a thorough examination of the fuel system. Check for signs of leaks, damage, or contamination. Inspect fuel lines, filters, and injectors for any obstructions that may hinder fuel flow. Using diagnostic tools can help identify issues more accurately.
Cleaning Fuel Filters: Regular maintenance includes cleaning or replacing fuel filters. Remove the filter and use an appropriate cleaning solution to eliminate debris. If the filter is excessively worn or damaged, it is advisable to replace it with a new one to ensure proper filtration.
Inspecting Fuel Injectors: Fuel injectors play a crucial role in delivering the right amount of fuel to the engine. Check the injectors for clogs or leaks. If necessary, clean the injectors using a specialized cleaning kit. For severely clogged injectors, replacement may be required.
Checking Fuel Lines: Inspect all fuel lines for cracks or wear. Any damaged lines should be replaced to prevent leaks. Ensure all connections are tight and free from corrosion to maintain an efficient fuel delivery system.
Testing Fuel Pressure: Utilize a fuel pressure gauge to test the pressure within the system. Low pressure may indicate a failing fuel pump or clogged lines. Address any discrepancies to ensure optimal performance.
Final Assembly and Testing: After performing all necessary maintenance tasks, reassemble the system. Start the engine and monitor for any irregularities. Ensure that there are no leaks and that the fuel delivery is consistent and efficient.
Steering System Adjustment Methods
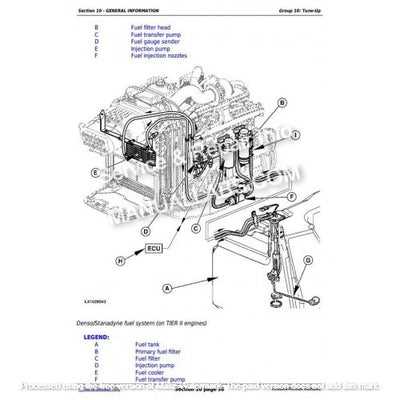
Proper alignment and calibration of the steering mechanism are essential for optimal vehicle handling and operator comfort. Ensuring that the steering system functions effectively can greatly enhance maneuverability and reduce wear on components. This section outlines various methods for achieving precise adjustments in steering systems.
Preliminary Inspection
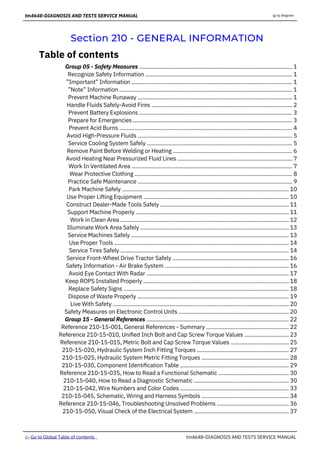
Before making any adjustments, it is crucial to perform a thorough inspection of the steering components. Check for signs of wear or damage, such as play in the steering wheel, loose connections, or worn-out bushings. Ensuring that all components are in good condition will prevent further issues during the adjustment process.
Adjustment Procedures
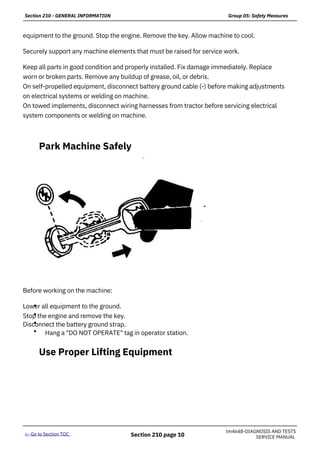
To achieve the desired steering response, follow these adjustment techniques:
1. Centering the Steering Wheel: Start by ensuring the steering wheel is centered when the vehicle is moving straight. Adjust the tie rods as needed to align the wheel position correctly.
2. Toe Alignment: Measure the distance between the front and rear of the tires on the same axle. Adjust the toe angle by turning the tie rod ends, ensuring that the wheels are parallel and properly aligned.
3. Camber and Caster Angles: Adjust the camber by changing the upper control arm settings. For caster, adjust the pivot points to achieve the desired angle, which influences steering stability.
Regular maintenance and proper adjustments of the steering system will contribute to enhanced performance and prolonged lifespan of the vehicle.
Brake System Maintenance Instructions
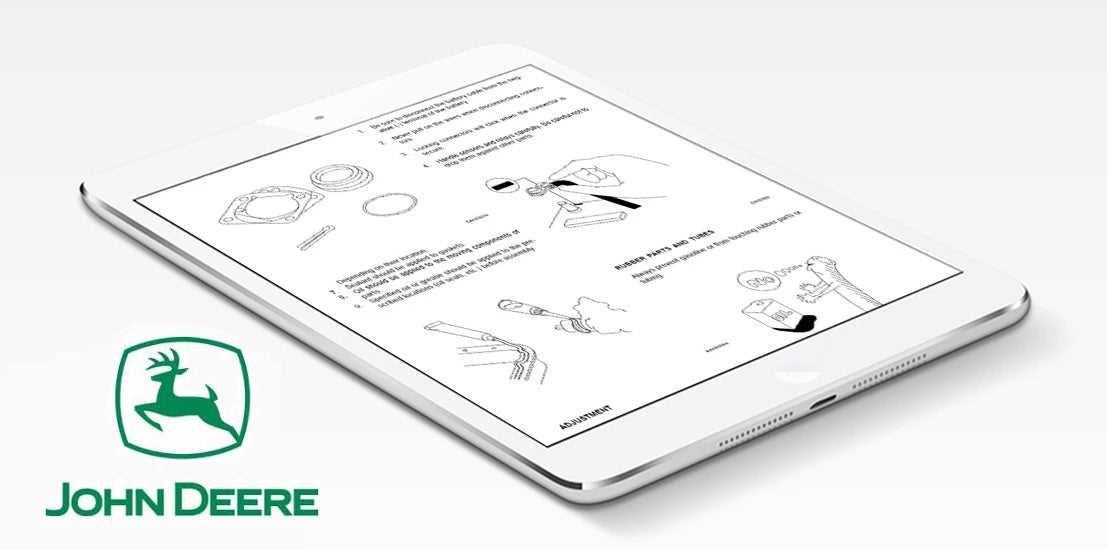
The brake system is crucial for the safe operation of any vehicle. Regular maintenance ensures optimal performance and extends the lifespan of the braking components. Proper care includes inspection, cleaning, and necessary adjustments to maintain effectiveness and safety on the road.
Key maintenance tasks include:
- Checking brake fluid levels and replacing as needed.
- Inspecting brake pads for wear and replacing them when they reach the manufacturer’s recommended thickness.
- Examining brake rotors for signs of damage or excessive wear.
- Ensuring that all brake lines and hoses are free from leaks and damage.
- Cleaning components to remove dust and debris that may affect performance.
Following these guidelines will help maintain the integrity of the brake system and promote safe operation.
Clutch Replacement and Adjustment
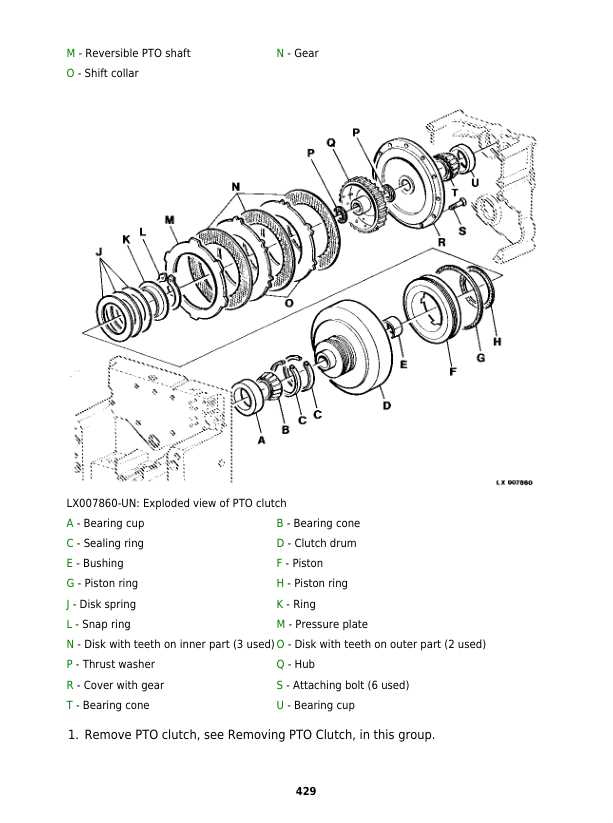
Replacing and adjusting the clutch is crucial for maintaining optimal performance and ensuring the longevity of the machinery. Proper engagement and disengagement of the clutch mechanism are essential for smooth operation and can prevent further mechanical issues.
Preparation for Clutch Replacement
Before starting the replacement process, it is important to gather the necessary tools and materials. Follow these steps to prepare:
- Ensure the equipment is parked on a level surface.
- Disconnect the battery to prevent accidental starts.
- Gather the required tools, including wrenches, screwdrivers, and a jack.
- Refer to the specific guidelines for any safety precautions related to the equipment.
Steps for Replacement and Adjustment
Follow these steps for the successful replacement and adjustment of the clutch:
- Remove the transmission cover to access the clutch assembly.
- Disconnect the linkage and any hydraulic connections attached to the clutch.
- Carefully detach the old clutch assembly from the flywheel.
- Inspect the flywheel for any damage and clean it if necessary.
- Install the new clutch, ensuring it is aligned correctly with the flywheel.
- Reconnect all linkages and hydraulic connections securely.
- Adjust the clutch engagement point according to the manufacturer’s specifications.
- Replace the transmission cover and reconnect the battery.
- Test the machinery to ensure proper function and engagement of the clutch.
Regular inspection and timely replacement of the clutch components will help maintain the efficiency and reliability of the equipment.
Wiring Diagram and Fuse Guide
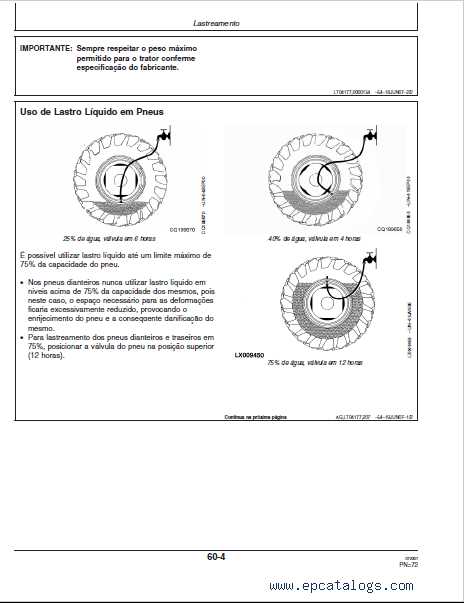
This section provides essential information regarding the electrical system and protective components of your machinery. Understanding the wiring layout is crucial for troubleshooting electrical issues, ensuring optimal performance, and maintaining safety standards.
The wiring diagram illustrates the connections between various electrical components, enabling you to identify the routes of power flow. Familiarity with this diagram aids in diagnosing faults, allowing for efficient repairs and modifications. Each wire is typically color-coded, which assists in tracing circuits and understanding their functions.
Additionally, the fuse guide outlines the specifications and locations of fuses within the system. Fuses serve as vital safety devices, protecting the electrical system from overloads and short circuits. It is important to know the correct ratings and types of fuses to replace, ensuring the longevity of your equipment and preventing potential damage.
Referencing both the wiring diagram and fuse guide regularly will facilitate better management of electrical issues, enhance understanding of the system’s operation, and ultimately contribute to the machinery’s reliability.