Internal Component Dusting: Use compressed air to remove dust from internal components, being careful to target hard-to-reach areas witho
Replacing Filters and Essential Parts
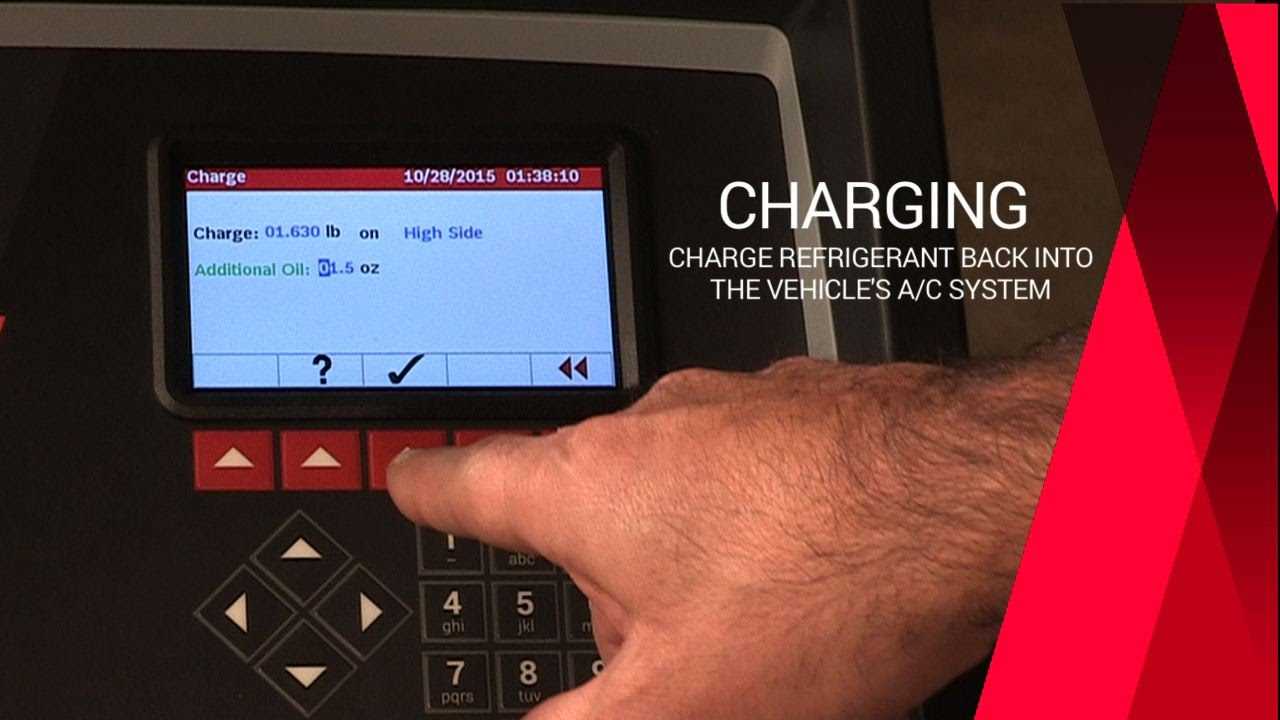
Regular replacement of filters and key components is crucial for maintaining optimal functionality and extending the equipment’s lifespan. Each part plays a unique role in preserving the unit’s performance, ensuring efficient operation and minimizing wear on other components. Proper upkeep of these parts not only supports reliable operation but also helps prevent unnecessary downtime.
When changing filters, begin by identifying the correct filter type and size, as these vary depending on the model. Carefully remove the old filter to avoid contaminating the internal areas. Once removed, inspect the housing for any debris or residue, and clean it as needed to ensure a proper seal for the new filter. Insert the replacement filter, ensuring it fits securely and aligns correctly to avoid leaks or reduced efficiency.
For other critical components, follow similar steps: identify the part, remove it with care, inspect for potential issues, and install the new piece with attention to fit and alignment. Replacing worn components in a timely manner can prevent larger issues, keeping the system operating smoothly and efficiently. It’s essential to use only compatible parts to ensure longevity and optimal performance.
Ensuring Proper Calibration of the Machine

Calibration is a crucial process that ensures the accuracy and reliability of any device used for measurement or analysis. Proper adjustments and checks are essential to maintain the optimal functioning of the equipment, enabling it to deliver precise results consistently. This section outlines the key steps and considerations involved in achieving effective calibration.
Understanding the Calibration Process
To achieve accurate measurements, it’s vital to follow a systematic calibration procedure. This typically involves comparing the device’s output against known standards and making necessary adjustments to eliminate discrepancies. Regular checks are important, as environmental factors can influence performance over time.
Regular Maintenance and Adjustments
In addition to initial calibration, ongoing maintenance is essential for sustained accuracy. Users should routinely inspect the machinery for signs of wear or damage, which can affect its performance. Implementing a schedule for regular calibration checks will help in identifying potential issues early, ensuring that the device remains in peak condition. Always refer to the manufacturer’s guidelines for specific maintenance recommendations to achieve the best results.
Troubleshooting Power and Connectivity Problems
When experiencing issues related to power and connectivity, it’s essential to systematically assess the components and connections involved. Identifying the root cause of these problems often involves a careful examination of both the power supply and the associated circuitry, ensuring that all connections are secure and functioning as intended.
Checking Power Supply
Start by inspecting the power source to ensure it is providing the correct voltage. Use a multimeter to measure the output and verify that it meets the required specifications. Additionally, examine any fuses or circuit breakers that may have tripped, as these can interrupt the flow of electricity and cause equipment to malfunction.
Inspecting Connections
Next, assess all cables and connectors for signs of wear or damage. Loose or corroded connections can lead to intermittent power issues or loss of connectivity. Ensure that all plugs are firmly seated in their respective sockets and consider cleaning contacts with an appropriate cleaner to enhance conductivity. If any cables appear frayed or compromised, replace them to prevent further issues.
Understanding Error Codes and Resolutions
Error codes are essential indicators that provide crucial information about the functionality of a device. They help users identify issues that may arise during operation, allowing for timely intervention and resolution. Understanding these codes can significantly enhance the efficiency of troubleshooting processes and ensure optimal performance.
Each code corresponds to a specific problem, and recognizing them is the first step toward resolving any malfunctions. Below are common error codes, their meanings, and suggested solutions:
-
Error Code 01: Indicates a low refrigerant level.
- Check for leaks in the system.
- Recharge with the appropriate refrigerant.
-
Error Code 02: Signals a temperature sensor malfunction.
- Inspect the sensor for proper placement and connection.
- Replace the sensor if it is damaged or non-functional.
-
Error Code 03: Suggests an electrical issue.
- Examine the wiring for any signs of wear or damage.
- Ensure all connections are secure and intact.
-
Error Code 04: Indicates an issue with the pressure readings.
- Calibrate the pressure gauges as needed.
- Check for blockages in the system that could affect readings.
It is crucial to address these error codes promptly to maintain the equipment’s efficiency and longevity. Always refer to the specific guidance provided for your device to ensure correct identification and resolution of issues.
Upgrading Software for Enhanced Functionality
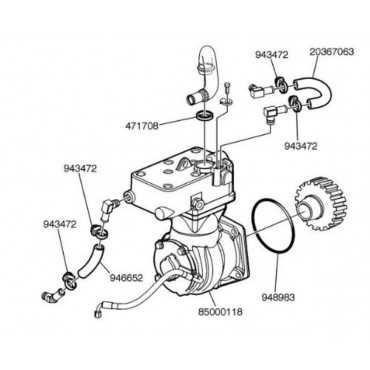
Updating software is essential for maintaining and improving the performance of any device. It can introduce new features, enhance security, and fix bugs that may hinder operations. Regularly revisiting the software version ensures that users can take full advantage of the latest technological advancements.
To effectively upgrade software, consider the following steps:
- Identify the current version: Knowing the existing software version helps determine if an update is necessary.
- Check for available updates: Visit the manufacturer’s website or use the built-in update feature to find the latest version.
- Read the release notes: Understanding what changes have been made can provide insight into the benefits of the upgrade.
- Backup data: Always create a backup of existing settings and configurations to prevent data loss during the upgrade process.
- Download the update: Ensure a stable internet connection and download the update package from a reliable source.
- Follow installation instructions: Adhere to the provided guidelines for a smooth installation experience.
- Restart the device: After installation, rebooting the device ensures that all changes take effect.
- Verify the upgrade: Confirm that the new software version is active and check for any immediate issues.
Regular software enhancements not only improve performance but also extend the lifespan of the equipment. By staying current with software upgrades, users can enjoy improved functionality and a more efficient operation.
Safety Practices During Machine Repair
Ensuring a secure environment while conducting maintenance tasks is paramount for both personal safety and the effective functioning of equipment. Adopting essential precautions not only mitigates risks but also enhances the overall efficiency of the workflow. Implementing proper safety measures creates a culture of vigilance that benefits everyone involved in the process.
Personal Protective Equipment (PPE)
Utilizing appropriate personal protective gear is crucial in minimizing exposure to potential hazards. Items such as gloves, safety glasses, and protective footwear should be standard in any workspace. Gloves protect against sharp edges and chemicals, while safety goggles shield the eyes from debris and harmful substances. Additionally, wearing steel-toed boots can prevent injuries from heavy objects falling or rolling.
Work Environment Considerations
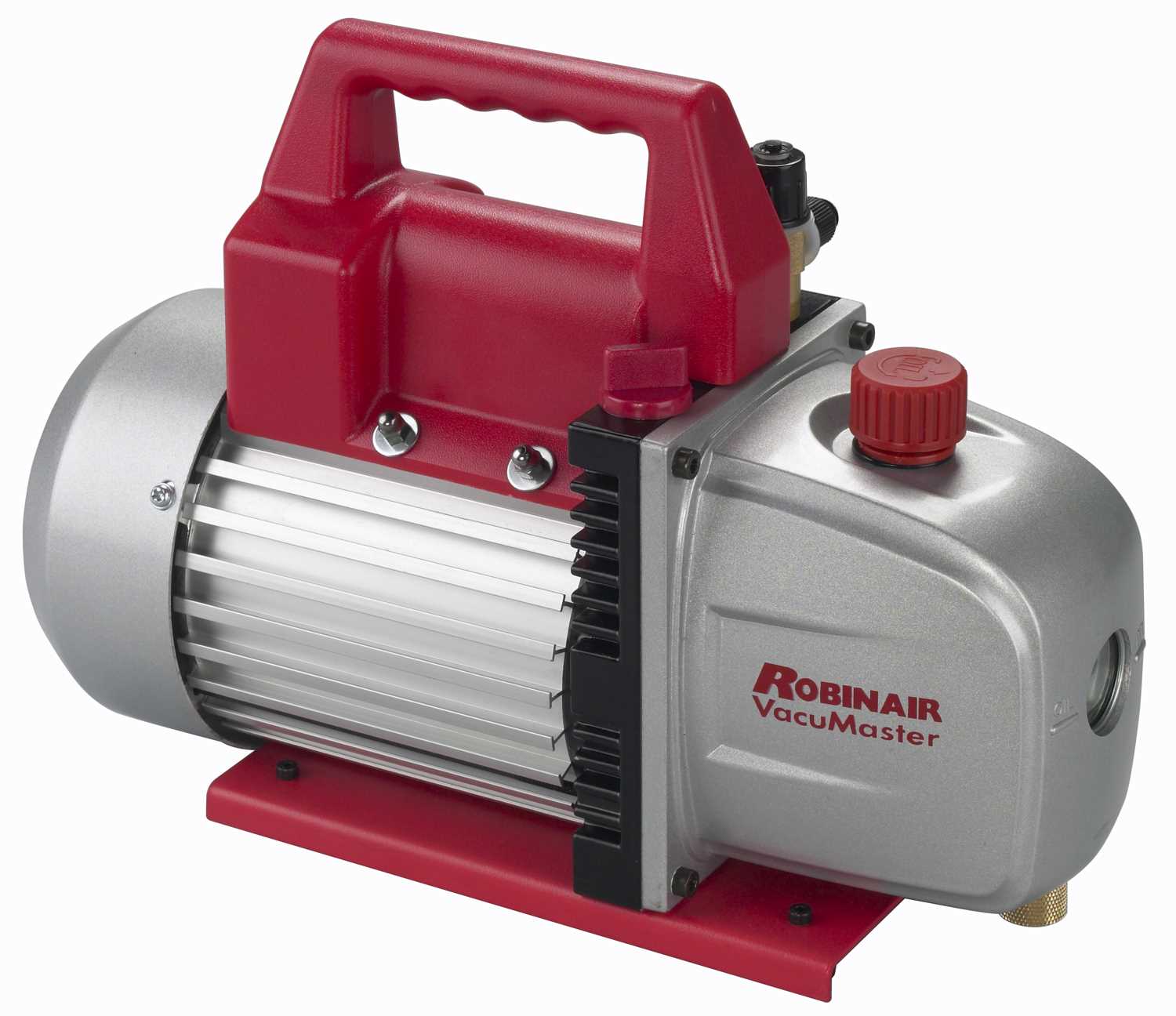
Maintaining an organized and clutter-free workspace is vital for safety. Ensuring that tools are stored properly and work areas are well-lit can significantly reduce the likelihood of accidents. It is also important to regularly inspect equipment for any signs of wear or damage. Implementing a routine check of all machinery and tools helps identify potential issues before they escalate, thus fostering a proactive approach to safety.
Where to Find Replacement Components
When it comes to maintaining equipment, sourcing replacement parts is crucial for ensuring longevity and optimal performance. This section explores various avenues for locating essential components that may need to be replaced over time. From online marketplaces to specialized suppliers, understanding where to look can significantly ease the repair process.
Online Marketplaces
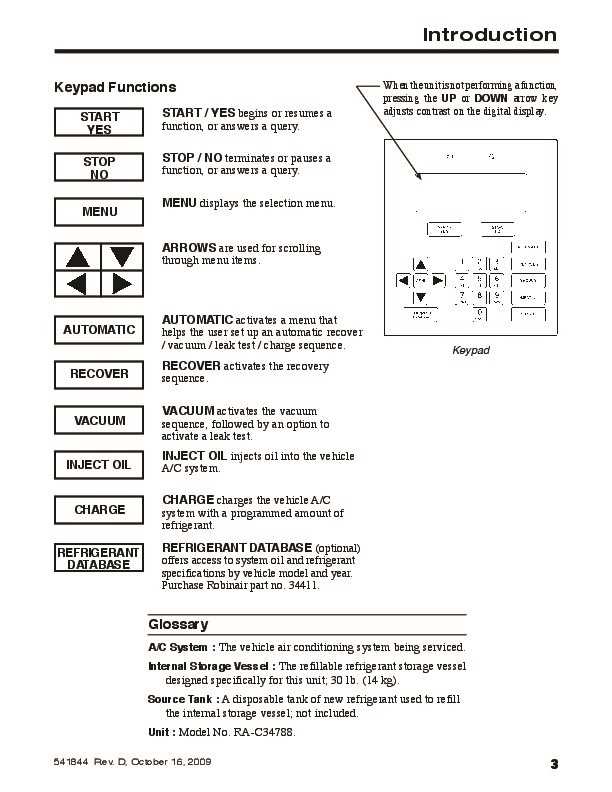
One of the most accessible ways to find components is through popular online platforms. Websites like eBay, Amazon, and dedicated electronics retailers offer a vast selection of parts. Here, users can often find new or refurbished items at competitive prices. It’s advisable to check the seller’s ratings and reviews to ensure reliability.
Specialized Suppliers
For more specific needs, consulting specialized suppliers can be beneficial. Many companies focus exclusively on parts for particular brands or types of equipment. These suppliers often provide high-quality components and valuable technical support. Below is a comparison of some reputable sources:
Supplier |
Website |
Specialization |
Supplier A |
www.supplierA.com |
General electronics |
Supplier B |
www.supplierB.com |
Automotive components |
Supplier C |
www.supplierC.com |
HVAC parts |