Maintenance Task |
Recommended Frequency |
Purpose |
Troubleshooting Ignition Problems
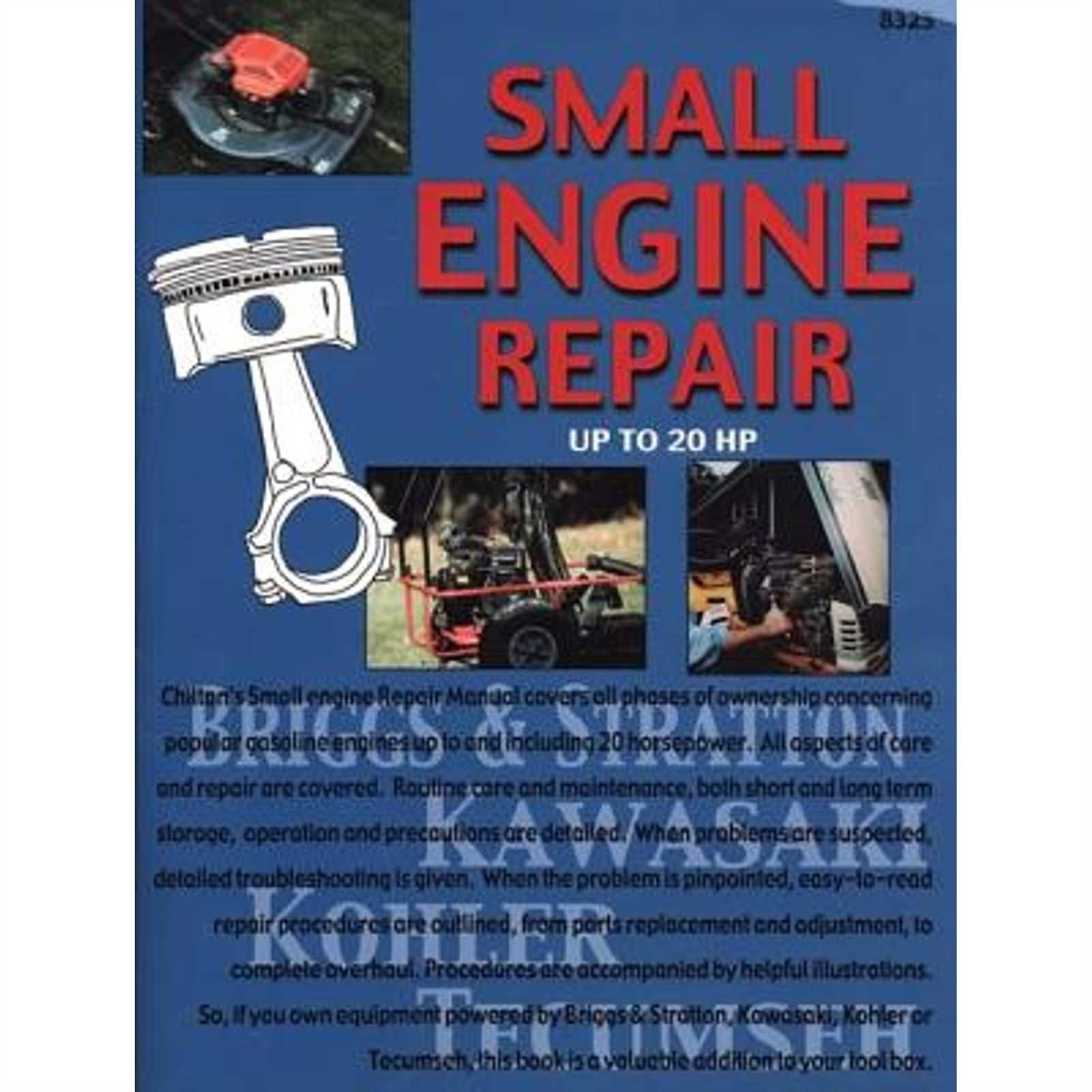
Addressing issues related to the ignition system is crucial for ensuring optimal performance and reliability of various machines. When ignition malfunctions occur, they can lead to starting difficulties or complete failure to operate. Identifying and resolving these problems promptly can enhance efficiency and extend the lifespan of the equipment.
Common Symptoms of Ignition Issues
- Engine fails to start
- Irregular or inconsistent operation
- Unusual sounds during operation
- Difficulty in maintaining power
Steps for Diagnosing Ignition Problems
- Check the power supply: Ensure that the battery is fully charged and the connections are secure.
- Inspect the spark plug: Examine for wear, carbon buildup, or damage, and replace if necessary.
- Examine ignition coil: Test the coil for continuity and inspect for any visible signs of damage.
- Review wiring and connections: Look for frayed wires, corrosion, or loose connections that could interrupt the electrical flow.
- Test ignition timing: Ensure that the timing is set correctly according to the manufacturer’s specifications.
By systematically following these steps, you can effectively identify and resolve ignition-related issues, ensuring that your equipment operates smoothly.
Guide to Carburetor Adjustment
The process of fine-tuning the fuel delivery system is crucial for optimal performance and efficiency. Proper adjustment ensures that the air-fuel mixture is balanced, which can significantly enhance the overall functionality of your machinery.
Understanding the Components is essential before beginning the adjustment. Familiarize yourself with the main parts of the system, including the float chamber, jets, and throttle plate. Each component plays a vital role in regulating fuel flow and air intake.
To achieve the best results, start with the basics. Begin by checking the existing settings, taking note of any irregularities. Use a reliable tool to measure the fuel level in the float chamber, as this can affect the mixture’s richness.
Adjusting the Air-Fuel Mixture involves turning the adjustment screws clockwise or counterclockwise. Small increments are recommended to prevent drastic changes that could lead to poor performance. After each adjustment, test the machine to observe any differences in operation.
Finally, perform a test run to ensure that the adjustments made are effective. Listen for any unusual sounds and monitor the machine’s responsiveness. Fine-tuning may require several iterations to achieve the desired performance.
Safety Precautions During Repairs
Ensuring a secure working environment is crucial when conducting maintenance on various machinery. Adopting proper safety measures can significantly reduce the risk of accidents and injuries. It is essential to be aware of potential hazards and to follow established protocols to protect oneself and others in the vicinity.
First and foremost, always wear appropriate personal protective equipment (PPE), such as gloves, safety glasses, and sturdy footwear. This gear serves as a barrier against harmful substances and sharp components. Additionally, maintain a clean workspace to minimize the chance of slips and falls.
Before commencing any tasks, disconnect power sources and ensure that all tools and equipment are in good condition. Familiarize yourself with the specific characteristics of the machinery you are working on to avoid unexpected complications. Moreover, follow the manufacturer’s guidelines and safety instructions diligently to ensure a smooth process.
It is advisable to keep a first aid kit accessible and to be familiar with basic emergency procedures. In case of an incident, knowing how to respond promptly can make a significant difference in outcomes. Lastly, consider working with a partner when tackling larger projects to provide assistance and support when needed.
Cleaning and Replacing Air Filters
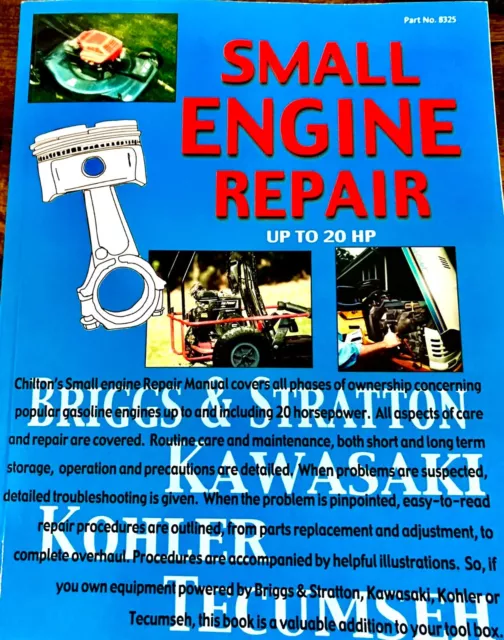
Maintaining optimal airflow is crucial for the efficient performance of various machinery. Regularly cleaning and replacing air filtration components can significantly enhance functionality and longevity. This section covers essential practices for ensuring these parts remain in excellent condition, contributing to the overall efficiency of the equipment.
Importance of Air Filters
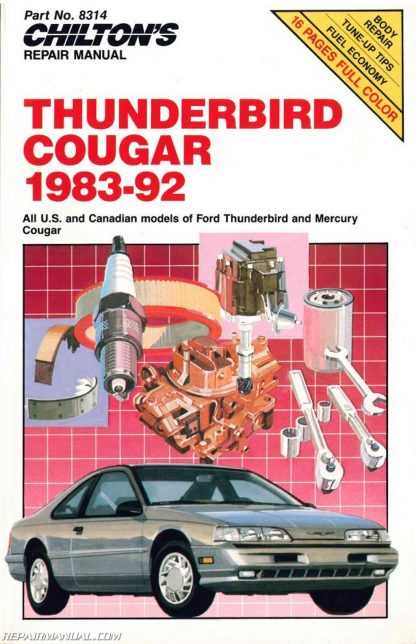
The air filter serves as a barrier, preventing dust and debris from entering critical internal components. A clean filter not only improves airflow but also aids in fuel efficiency and reduces emissions. Neglecting this maintenance task can lead to performance issues and increased wear on other parts.
Steps for Cleaning and Replacement
Begin by identifying the location of the air filter. Once located, carefully remove it following the manufacturer’s guidelines. For cleaning, gently tap the filter to dislodge loose particles or use compressed air for a more thorough approach. If the filter is excessively dirty or damaged, replacement is necessary. Ensure you install a compatible new filter securely to maintain proper airflow.
Regular checks and maintenance of air filtration systems are essential practices that help in preserving equipment performance and extending its lifespan.
Steps to Improve Engine Efficiency
Enhancing the performance of your machinery involves several strategic approaches that can lead to significant benefits. By implementing various techniques, users can maximize productivity while minimizing fuel consumption. This section outlines effective practices that can contribute to optimizing functionality.
Regular Maintenance
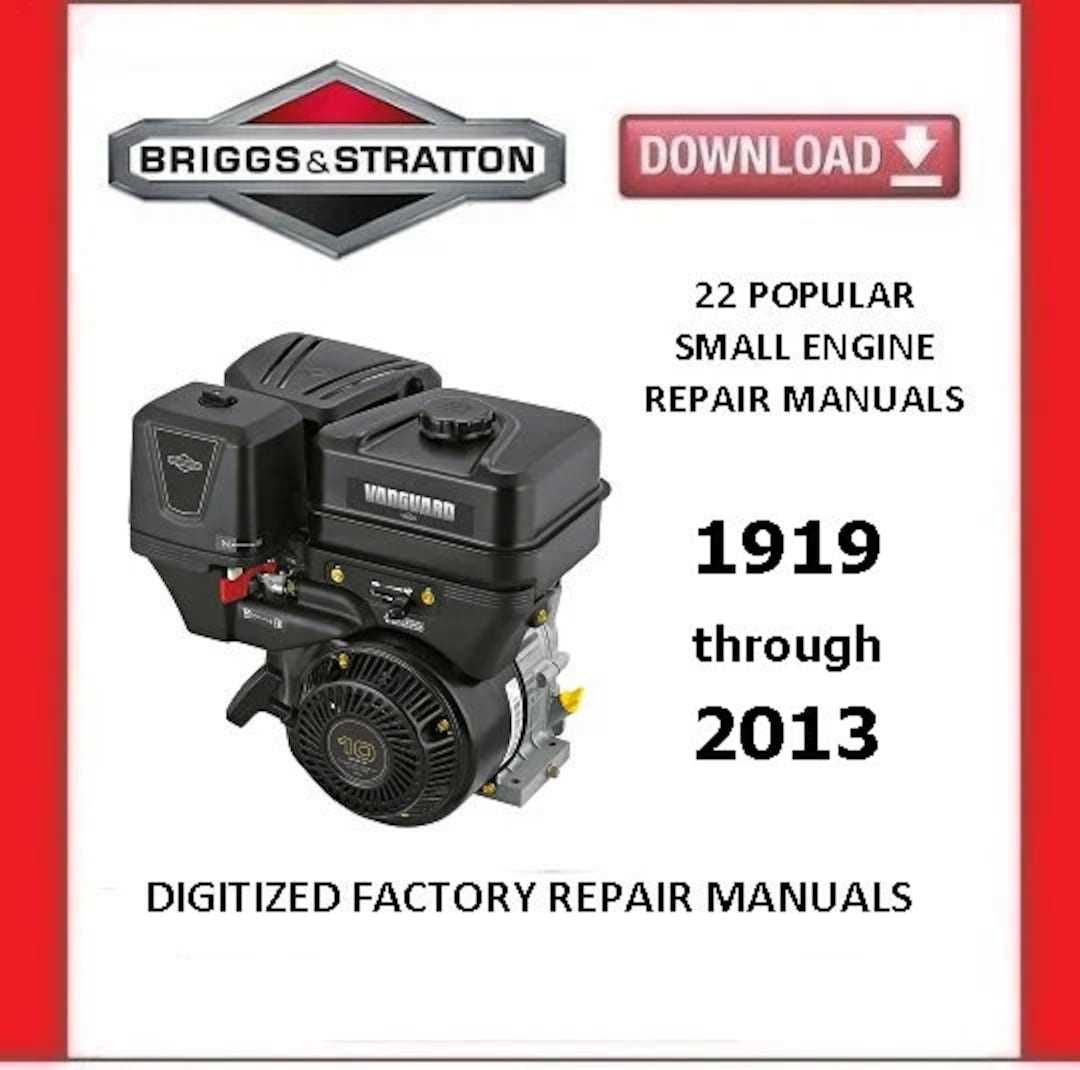
Routine upkeep is crucial for ensuring that all components are functioning optimally. Regularly checking and replacing filters, as well as keeping spark plugs clean, can help maintain peak performance. Additionally, adhering to suggested schedules for oil changes will greatly influence overall efficiency.
Optimal Fuel Use
Using the right type of fuel can greatly enhance efficiency. High-quality fuels can improve combustion and reduce the likelihood of deposits forming within the system. Furthermore, adjusting fuel-to-air ratios according to the manufacturer’s specifications can lead to improved performance and lower emissions.
Inspecting and Fixing Fuel Systems
Proper assessment and maintenance of fuel systems are essential for optimal performance and longevity of various machinery. This section will explore the vital steps to evaluate and resolve issues related to fuel delivery and management. Understanding the components involved and recognizing potential problems can significantly enhance the reliability of your equipment.
Key Components of Fuel Systems
- Fuel Tank
- Fuel Pump
- Fuel Filter
- Carburetor or Fuel Injector
- Fuel Lines
Steps for Inspection and Maintenance
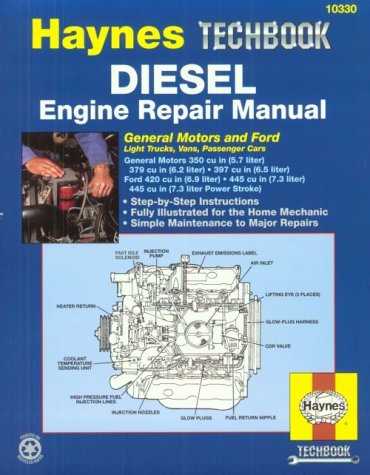
- Check for fuel leaks around the tank, lines, and connections.
- Inspect the fuel filter for clogs or contamination and replace it if necessary.
- Ensure the fuel pump is functioning correctly by listening for unusual noises during operation.
- Examine the carburetor or fuel injector for signs of wear and ensure proper adjustment.
- Clean or replace any corroded or damaged fuel lines.
Regular inspection and timely repairs of fuel systems will help in maintaining performance and preventing costly failures. Following these guidelines ensures that your machinery operates efficiently and reliably.
Choosing Quality Replacement Parts
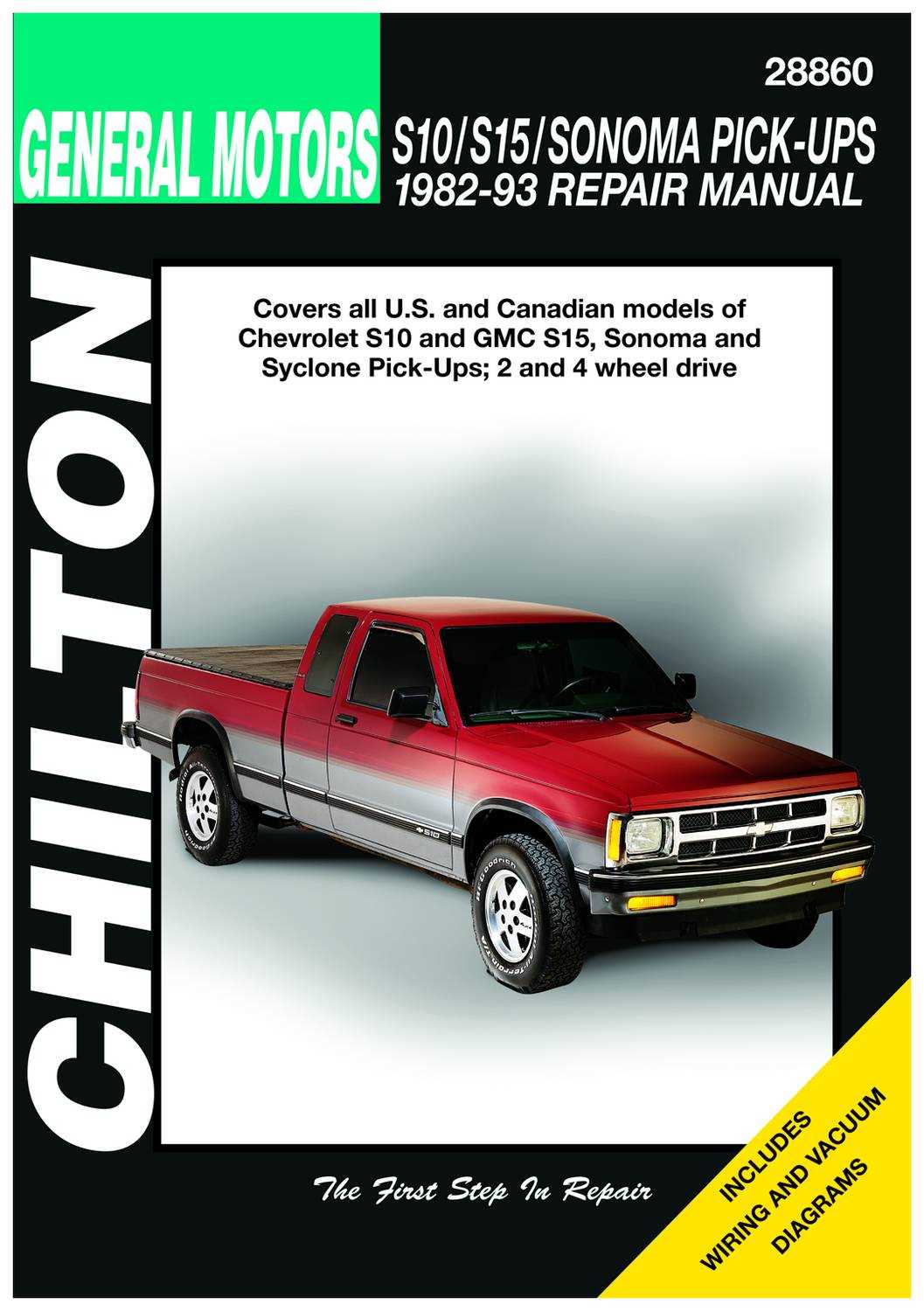
Selecting top-notch components is essential for ensuring the longevity and performance of machinery. The quality of these parts can significantly influence how well the equipment functions and how long it lasts. Therefore, making informed decisions when sourcing replacements is crucial for any maintenance or enhancement project.
First and foremost, it’s vital to consider the compatibility of the parts with your specific machinery. Using components that are designed to fit perfectly can prevent issues such as improper functioning or accelerated wear. Researching specifications and manufacturer recommendations can help in this regard.
Additionally, investing in reputable brands often pays off in the long run. Well-known manufacturers typically provide higher quality and durability. While they might come at a slightly higher cost, the reliability they offer can save you from frequent replacements and repairs.
Finally, don’t forget to read customer reviews and seek recommendations. Feedback from others who have used similar parts can provide valuable insights into their performance and longevity. Making educated choices based on both specifications and user experiences will lead to more successful outcomes in your projects.
Preventative Care for Small Engines
Maintaining optimal performance and extending the lifespan of machinery requires regular attention and upkeep. A proactive approach ensures that potential issues are identified and addressed before they escalate, thus enhancing reliability and efficiency.
Routine inspections are crucial for detecting early signs of wear and tear. Checking components such as filters, belts, and spark plugs regularly can prevent minor problems from developing into major repairs. Keeping these elements clean and in good condition not only improves functionality but also enhances safety during operation.
Additionally, proper lubrication is vital to ensure smooth operation. Utilizing the right type and amount of oil minimizes friction and reduces the risk of overheating. Adhering to the manufacturer’s specifications regarding lubrication intervals helps maintain optimal performance.
Another essential aspect is fuel quality. Using fresh, clean fuel prevents clogs and other issues associated with stale gasoline. Storing fuel properly and using stabilizers can significantly improve longevity and performance.
Lastly, environmental factors should not be overlooked. Protecting machinery from extreme weather conditions, moisture, and dust can greatly reduce wear and prolong service life. Implementing these simple yet effective strategies contributes to the longevity and reliability of your equipment.