Addresses
Replacing Damaged Transmission Components
Efficient component replacement is essential to maintain smooth operation and extend the lifespan of the system. Identifying parts that show wear or have sustained damage allows for timely interventions, helping avoid further complications. Carefully assess each element’s condition to determine whether replacement is necessary.
Step 1: Preparation and Inspection
Begin by ensuring the system is fully disengaged and safely secured. Examine each part thoroughly, focusing on visible signs of wear, cracks, or alignment issues. Look for any components that may appear loose or misaligned, as these are indicators that replacement might be required.
Step 2: Selecting Compatible Parts
When choosing replacement parts, prioritize compatibility to ensure a smooth fit with existing components. Using well-matched elements reduces installation time and prevents potential issues. If unsure, consult trusted sources or documentation to confirm each part’s specifications.
Step 3: Safe Removal and Installation
For each damaged piece, use proper tools to carefully detach it from its assembly. Follow a steady, organized approach to keep parts aligned and avoid damaging nearby components. Once the worn part is removed, position the new piece with precision, securing it according to standard installation procedures.
In
How to Troubleshoot Electrical Connections
Maintaining optimal functionality in complex machinery often hinges on the integrity of electrical links. When issues arise, pinpointing the root causes requires a systematic approach to identifying faults within these connections. Understanding common symptoms and employing effective diagnostic strategies can lead to successful resolution.
Common Symptoms of Electrical Issues
Identifying indicators of electrical malfunctions is crucial for timely intervention. Look for signs such as intermittent operation, failure to engage, or unusual noises. Additionally, visual inspections can reveal corrosion, loose connectors, or damaged wiring, which often contribute to connectivity problems.
Diagnostic Steps to Follow

To accurately diagnose electrical issues, follow these essential steps:
Step |
Description |
1 |
Perform a visual inspection of all connections and wiring for signs of wear or damage. |
2 |
Use a multimeter to test continuity across terminals and connectors. |
3 |
Check for proper voltage levels at various points in the system. |
4 |
Inspect grounding points to ensure they are secure and free from corrosion. |
5 |
Consult schematic diagrams for reference to wiring configurations and pinpoint potential discrepancies. |
By adhering to these guidelines, you can effectively troubleshoot electrical connections and restore proper operation.
Inspecting Sensors and Actuators
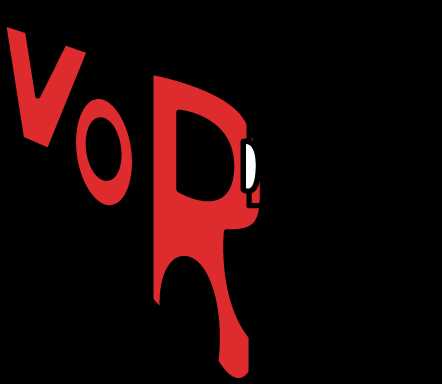
Regular examination of the components responsible for system feedback and control is essential for optimal performance. These elements play a critical role in ensuring that various operations are executed accurately and efficiently. Identifying any potential issues early can prevent more significant problems down the line.
Understanding Functionality
Each sensor and actuator operates based on specific principles. Sensors detect changes in conditions such as pressure, temperature, or position, while actuators are responsible for executing commands by controlling movement or regulating flow. Familiarity with their functionalities aids in diagnosing malfunctions.
Inspection Techniques
When inspecting these components, it is vital to perform visual checks for any signs of wear, damage, or disconnections. Utilizing diagnostic tools can provide deeper insights into their operational status. Monitoring signal outputs and comparing them with expected values is crucial for identifying discrepancies.
Maintenance Practices
Implementing routine maintenance can extend the lifespan of these critical components. Cleaning contacts and ensuring proper alignment during reinstallation are recommended practices. Additionally, keeping connections secure will help maintain consistent performance and reduce the likelihood of future complications.
Preventative Maintenance Tips for I-Shift
Ensuring the longevity and optimal performance of your vehicle’s automated gear system requires regular attention and care. By following some essential maintenance practices, you can help prevent potential issues and enhance the reliability of your vehicle’s drive system.
Regular Fluid Checks
Fluid quality and levels play a crucial role in the functionality of the automated gear system. Check the fluid at regular intervals to ensure it remains at the recommended levels and is free from contaminants. If the fluid appears dirty or has an unusual odor, consider replacing it to maintain efficient operation.
Routine Software Updates
Keeping the control software up to date is essential for optimal performance. Manufacturers often release updates that improve efficiency and address any known issues. Regularly check for software upgrades and install them as recommended to ensure your vehicle operates smoothly and effectively.
Resetting I-Shift Control Parameters
Recalibrating the control settings of an automated driving system is crucial for maintaining optimal performance. This process involves adjusting the parameters that govern how the system responds to various driving conditions, ensuring a smooth and efficient operation.
Step-by-Step Process: To initiate the recalibration, first ensure that the vehicle is on a level surface and the engine is turned off. Next, access the vehicle’s diagnostic interface using specialized software or tools designed for this purpose. Once connected, navigate to the control settings menu where the current parameters can be viewed and modified.
After reviewing the existing settings, reset them to their factory defaults if any inconsistencies are detected. This step is essential for eliminating any previous adjustments that may affect functionality. Following the reset, input the desired custom parameters tailored to the specific operational needs and driving conditions.
Finally, save the new settings and conduct a test drive to verify that the recalibrated parameters are functioning as intended. Monitoring the system’s response during the drive will help ensure that the adjustments have been successful and the automated driving capabilities are performing optimally.
Best Practices for Calibration
Achieving optimal performance in automated systems requires precise adjustments and settings. This section outlines essential techniques to ensure accuracy and reliability during the calibration process. Implementing these practices can enhance functionality and prolong the lifespan of equipment.
Before commencing any calibration procedure, it is crucial to prepare adequately. Gathering the necessary tools, understanding the system specifications, and familiarizing oneself with the calibration steps are fundamental. Proper training and knowledge of the equipment help minimize errors and increase efficiency.
Regular maintenance of the calibration tools is also vital. Keeping instruments clean, well-calibrated, and stored appropriately can significantly impact the overall accuracy of the calibration process.
Practice |
Description |
Documentation |
Maintain detailed records of all calibration procedures, settings, and results for future reference. |
Environment Control |
Ensure the calibration environment is stable in terms of temperature, humidity, and cleanliness to avoid external influences on the results. |
Incremental Adjustments |
Make small, gradual changes to settings rather than large adjustments, which can lead to overshooting the desired outcome. |
Verification |
After calibration, verify the results against known standards to confirm accuracy and reliability. |
By following these guidelines, one can achieve effective and efficient calibration, ensuring that the automated systems function as intended.
Testing Transmission Performance Post-Repair
After completing the necessary adjustments and enhancements to the gear mechanism, it is essential to assess its functionality to ensure optimal operation. This evaluation focuses on several key aspects, including responsiveness, efficiency, and overall performance under various driving conditions. Proper testing not only verifies that the system is functioning as intended but also identifies any potential issues that may need addressing.
Initial Evaluation
Start by conducting a preliminary assessment to check for any unusual noises or vibrations when engaging the system. It is crucial to monitor how the device responds during gear changes, paying close attention to the smoothness and timing of shifts. Documenting these observations will help in analyzing performance trends over time.
Performance Testing
Following the initial assessment, perform a series of controlled tests to evaluate the unit’s functionality under different scenarios. This may include measuring acceleration, deceleration, and the ability to maintain power delivery under load. Using diagnostic tools can provide valuable insights into the internal workings of the mechanism, allowing for a more precise evaluation of its state. Regular performance checks are vital for ensuring longevity and reliability in any application.
Long-Term Care for I-Shift Systems
Maintaining the longevity of automated gear systems is essential for optimal performance and reliability. Regular attention to various components can prevent issues and enhance the overall lifespan of the vehicle. This section outlines key practices to ensure these systems remain in excellent condition over time.
- Regular Fluid Checks: Monitoring fluid levels and quality is crucial. Ensure that the hydraulic fluid is clean and at the appropriate level to facilitate smooth operation.
- Scheduled Maintenance: Adhere to the recommended service intervals. Routine inspections help identify wear and tear before they lead to significant problems.
- Software Updates: Keep the control software up to date. Manufacturers often release updates that enhance performance and address known issues.
- Component Inspections: Periodically inspect components such as sensors, actuators, and connectors for any signs of damage or wear. Early detection can prevent larger malfunctions.
- Driving Habits: Encourage smooth driving practices. Abrupt accelerations and hard braking can stress the system, leading to premature wear.
By following these practices, you can significantly extend the service life of automated gear systems, ensuring they operate efficiently and reliably for years to come.
|