Facilitates secure and stable connections, especially f
Testing Input and Output Voltages
Understanding how to test the input and output voltages is essential for evaluating the functionality and stability of electrical units. Measuring these voltages accurately helps identify potential issues in the circuit, ensuring components receive appropriate levels of electrical flow.
Input voltage testing involves checking the incoming electrical levels, ensuring that they align with expected standards. Begin by setting the multimeter to the correct range, then connect the probes to the input terminals. Compare the measured values with specified requirements to confirm proper energy delivery.
Output voltage testing focuses on verifying that each connection point provides the correct voltage to downstream elements. This step often requires measuring multiple terminals to assess if each pathway is supplying the expected electrical output. Note any discrepancies in readings, as these could indicate internal faults or potential interruptions within the circuitry.
Maintaining accuracy in voltage tests is crucial. Double-check connections, and ensure that all equipment is properly calibrated before performing any measurements to prevent misinterpretation of results.
Replacing Blown Fuses and Components
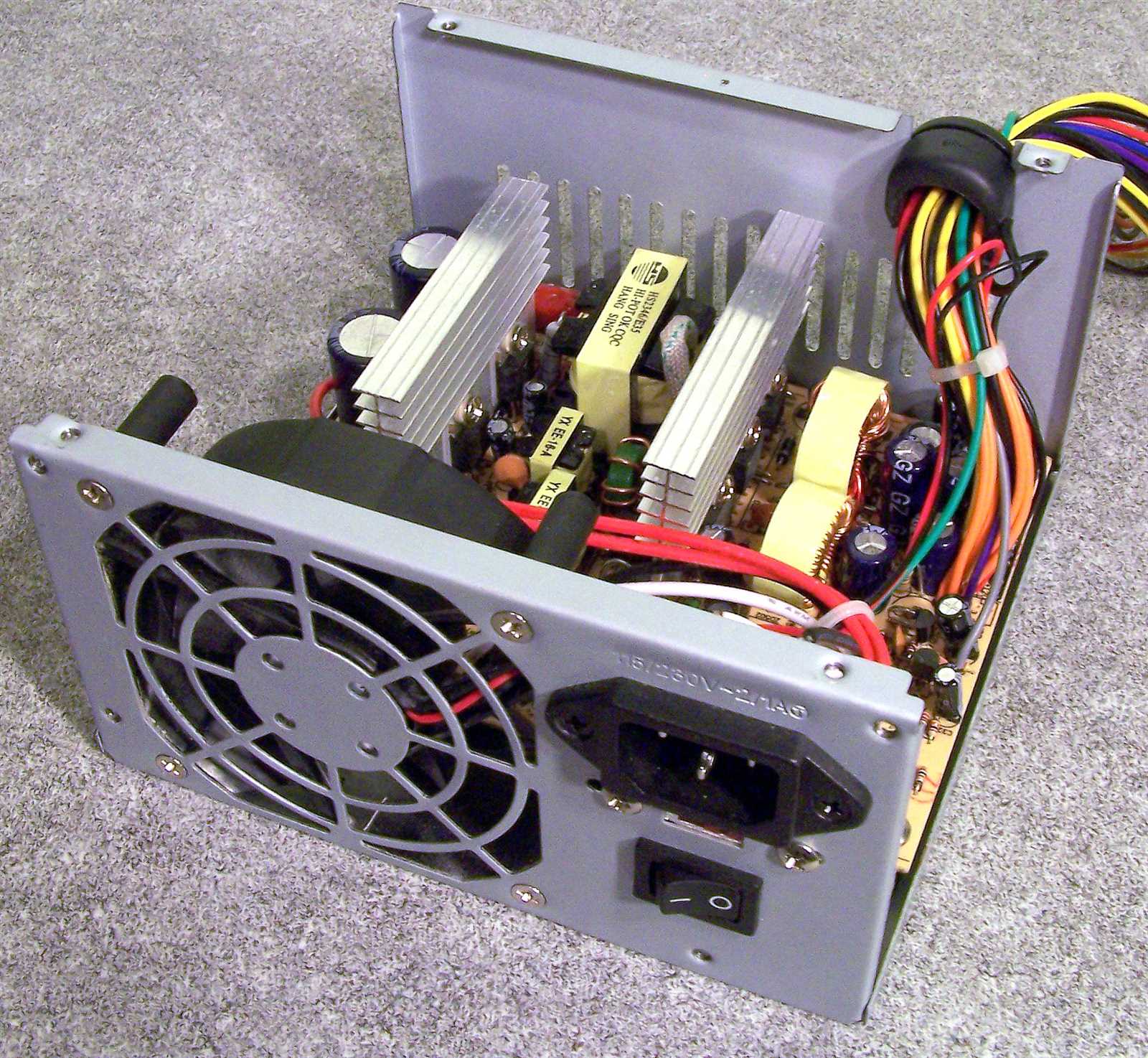
In certain electronic modules, blown fuses and damaged elements can lead to sudden shutdowns or failures. Identifying and replacing these parts helps restore function, ensuring a stable and safe operation. This section guides you through locating faulty components, testing them, and safely replacing them with suitable replacements.
The process of replacing fuses and other small elements requires attention to detail and a systematic approach. To get started, follow these essential steps:
- Identify Blown Fuses: Look for any visible signs of damage, such as discoloration or broken filaments within the fuse. Using a multimeter, check for continuity to confirm if the fuse is functional or needs replacement.
- Locate Faulty Components: Examine other visible parts, such as capacitors or resistors, for signs of burning, leaking, or swelling. Components showing physical damage or unusual wear should be tested and, if necessary, replaced.
- Select Suitable Replacements: When replacing any component, ensure that the new part matches the original’s specifications to avoid compatibility issues. Consult the schematic or part number to find the correct ratings and values.
- Install with Caution: Carefully desolder the damaged part, clean the contact points, and install the new component. Ensure proper alignment, and check that all connections are secure before reassembling.
After replacing the damaged elements, perform a final inspection to confirm all connections are stable and free from potential short circuits. Testing the unit before full reassembly can help confirm a successful repair.
Diagnosing Short Circuits and Overloads
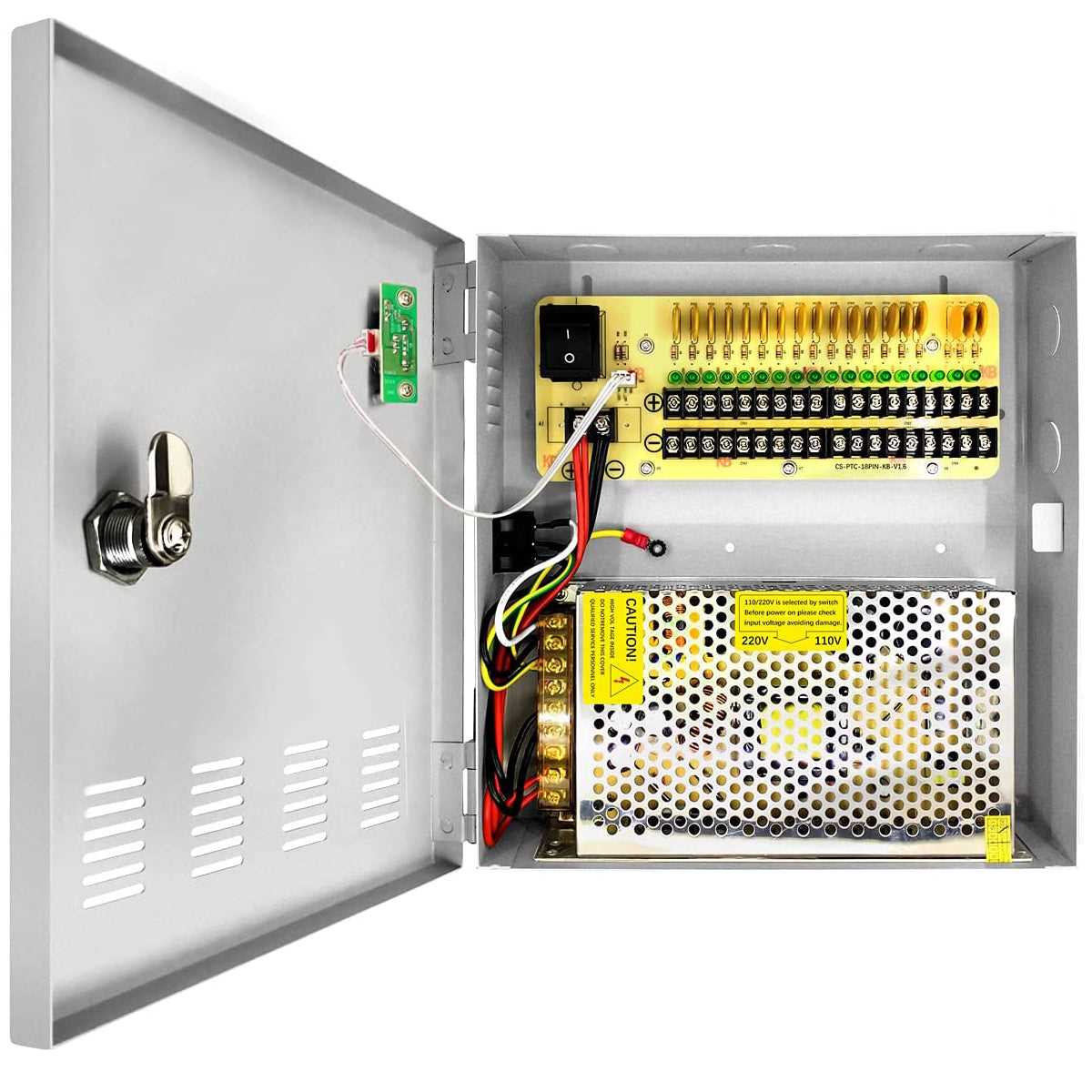
Identifying electrical faults is crucial in ensuring the longevity and functionality of various devices. Short circuits and overloads can lead to significant operational failures if not addressed promptly. This section outlines the methods and tools necessary for effective diagnosis, enabling users to troubleshoot and mitigate potential issues before they escalate.
Understanding the Symptoms
Recognizing the early indicators of electrical faults is essential for efficient troubleshooting. Common symptoms include unusual noises, excessive heat, and frequent disconnections. Below is a table summarizing typical signs and their possible causes:
Symptom |
Possible Cause |
Unusual Sounds |
Loose connections or failing components |
Overheating |
Excessive current draw or inadequate ventilation |
Frequent Tripping |
Overload conditions or short circuits |
Utilizing Testing Tools
Employing the right tools can significantly enhance the diagnostic process. Multimeters, oscilloscopes, and current clamps are invaluable for measuring voltage, current, and resistance. Using these devices, one can trace the source of faults effectively and accurately. Regular testing and maintenance can prevent potential failures, ensuring optimal performance of the device.
Fixing Unstable Power Output Issues
Inconsistent energy delivery can lead to various performance problems in electronic devices. Identifying the root causes of fluctuations is essential to restoring stability and ensuring the reliability of your system. This section explores common issues and provides insights into addressing them effectively.
One frequent culprit behind unstable energy distribution is capacitor failure. These components play a crucial role in smoothing voltage levels, and when they degrade, it can lead to erratic behavior. Inspecting capacitors for signs of bulging or leakage is a good starting point. If any issues are found, replacing them with equivalent or higher-rated components can often rectify the situation.
Another aspect to consider is the quality of the connections. Loose or corroded terminals can interrupt the flow of electricity, resulting in variability. It’s advisable to thoroughly check all connections, ensuring they are tight and free of oxidation. Cleaning the contact points with appropriate solvents can enhance conductivity.
Below is a table summarizing common causes of unstable energy output and potential solutions:
Cause |
Solution |
Capacitor Failure |
Inspect and replace damaged capacitors |
Poor Connections |
Tighten and clean terminals |
Overloading |
Reduce load or upgrade components |
Faulty Components |
Test and replace malfunctioning parts |
By addressing these issues methodically, you can enhance the stability of your device’s energy delivery, ultimately prolonging its lifespan and improving performance.
Cleaning and Preventing Dust Buildup
Maintaining the internal cleanliness of electronic devices is crucial for their optimal performance and longevity. Accumulation of particulate matter can lead to overheating and inefficient functioning, making regular maintenance an essential practice. Implementing proper cleaning techniques and preventive measures can significantly reduce dust accumulation, ensuring smooth operation and extending the lifespan of the components.
To effectively manage dust, it is advisable to adhere to a consistent cleaning schedule. The following table outlines recommended cleaning practices and their frequency:
Cleaning Practice |
Frequency |
External Wipe Down |
Weekly |
Internal Component Cleaning |
Every 3-6 months |
Filter Replacement or Cleaning |
Monthly |
Environmental Control (Humidity, Temperature) |
Ongoing |
By integrating these cleaning routines and monitoring the environment where the device is housed, users can create an optimal atmosphere that minimizes dust buildup. Employing air purifiers and maintaining proper ventilation can further assist in achieving a cleaner operating environment.
Managing Heat and Cooling Systems
Effective thermal management is essential for maintaining optimal performance and longevity of electronic devices. By controlling temperature levels, it is possible to prevent overheating, which can lead to component failure or reduced efficiency. Implementing a well-designed cooling strategy can significantly enhance the overall reliability and functionality of the system.
Several techniques can be employed to manage heat effectively. Passive cooling methods, such as heat sinks and thermal pads, dissipate heat without the need for power consumption. Active cooling solutions, including fans and liquid cooling systems, provide more aggressive temperature control by actively circulating air or coolant. Selecting the appropriate method depends on the specific requirements and constraints of the application.
In addition to cooling solutions, proper airflow design within the enclosure plays a crucial role in heat management. Ensuring adequate ventilation and strategic placement of components can promote effective heat dissipation. Regular maintenance, such as cleaning dust and debris from cooling components, is also vital to maintain system efficiency and prevent overheating.
Finally, monitoring temperature levels with sensors can provide real-time data to assess the effectiveness of the cooling strategy. This feedback allows for adjustments and optimizations to be made, ensuring that the system operates within safe temperature ranges. Overall, a proactive approach to heat management can lead to improved performance and extended service life of electronic devices.
Reassembling and Securing the Unit Properly
Restoring the integrity of the device after disassembly is crucial for its optimal performance and longevity. Ensuring that each component is correctly positioned and securely fastened prevents potential malfunctions and hazards. The following guidelines will assist in this essential phase of the process.
- Verify Components:
Before starting the reassembly, double-check that all parts are intact and functional. This includes:
- Connectors
- Capacitors
- Cooling fans
- Wires and cables
- Organize the Workspace:
Keep your workspace tidy and free from any clutter to avoid losing small components. Use trays or containers to separate screws and parts.
- Follow the Original Layout:
Refer to documentation or photographs taken during disassembly to ensure each component is reinstalled in the correct location.
- Secure Connections:
As you reattach each element, make sure all connectors are firmly in place. Check that there are no loose wires that could cause short circuits.
- Fasten the Housing:
Once all internal components are in position, carefully place the outer casing back on. Ensure all screws are tightened properly to maintain the structure’s integrity.
- Test the Assembly:
After everything is reassembled, conduct a preliminary test to confirm that the unit operates correctly before returning it to use.
By adhering to these steps, you can ensure that the restoration process is conducted efficiently, resulting in a reliable and safe device ready for operation.
Safety Precautions and Final Testing
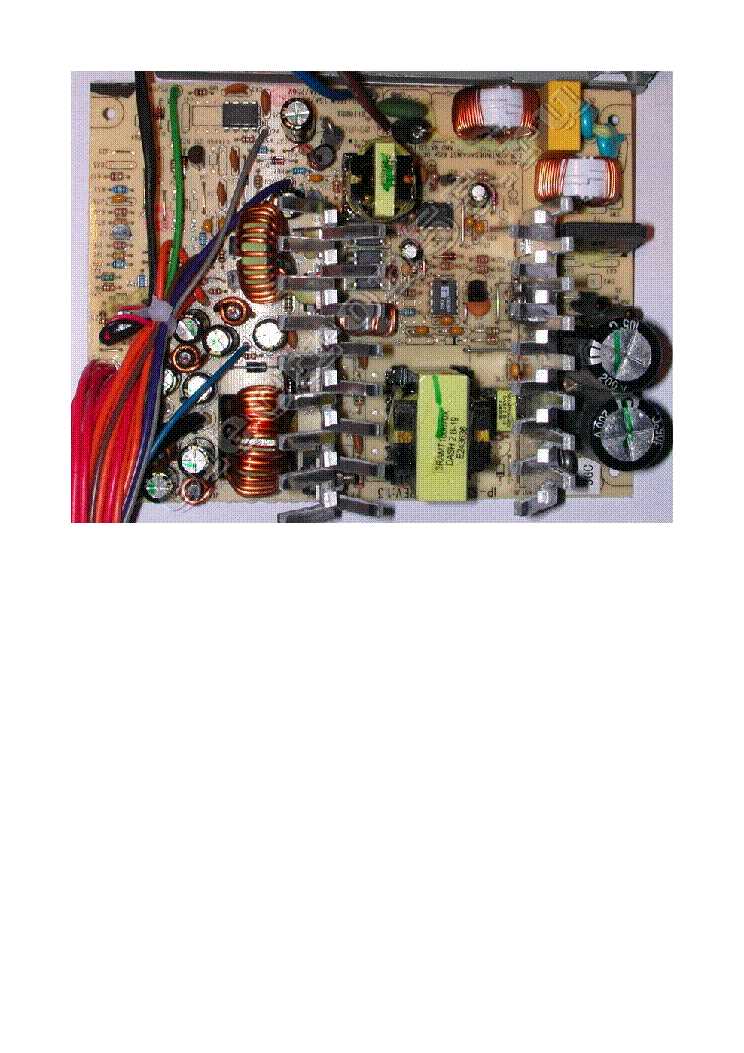
Ensuring the safety of both the technician and the device is paramount during the maintenance process. Adhering to proper guidelines minimizes risks associated with handling electrical equipment and enhances the reliability of the final product.
Before initiating any work, it is crucial to follow these safety measures:
- Disconnect the device from any power source to prevent electrical shocks.
- Use insulated tools to reduce the risk of accidental short circuits.
- Work in a well-ventilated area to avoid exposure to potentially harmful fumes.
- Wear safety goggles and gloves to protect against unexpected hazards.
- Keep flammable materials away from the workspace to prevent fires.
Once the necessary adjustments or replacements have been completed, conducting thorough testing is essential to verify the integrity and functionality of the unit. Follow these steps for final assessments:
- Reassemble the device carefully, ensuring all connections are secure.
- Reconnect it to a suitable power source while keeping a safe distance.
- Monitor for any unusual sounds or smells during the initial power-up.
- Check voltage outputs with a multimeter to confirm they meet specifications.
- Perform load tests to ensure stability under normal operational conditions.
Following these precautions and testing protocols not only enhances safety but also ensures the longevity and effectiveness of the repaired equipment.
|