Soaking: Place parts in lukewarm, soapy water for around 10-
Maintaining Woodwind Instrument Components
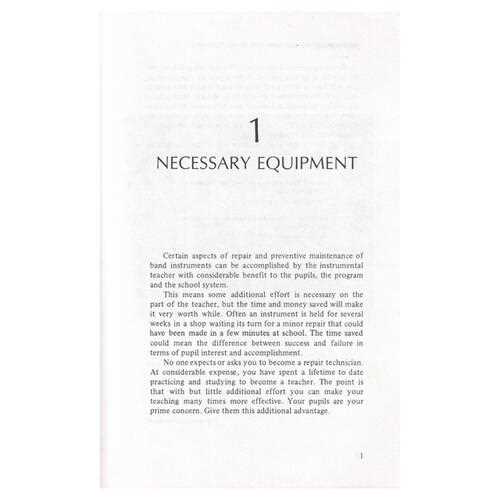
Proper upkeep of woodwind parts ensures a lasting, quality sound and prevents issues during play. Regular attention to essential elements can significantly improve the longevity and performance of these parts. Key areas of focus include preserving wood and metal sections, caring for delicate pads, and ensuring smooth operation of moving pieces.
Wood and Metal Parts: Keep wood sections moisturized by using appropriate oils sparingly. Avoid exposure to extreme temperatures and humidity, which can cause cracking or warping. Metal pieces benefit from periodic cleaning with a soft cloth to remove moisture and fingerprints that may cause corrosion.
Pads and Corks: Pads require gentle handling as they are essential for creating an airtight seal. Avoid excess moisture, and clean only with recommended tools. Corks should be lubricated with cork grease periodically to maintain flexibility and prevent drying out.
Repairing Key Mechanisms in Woodwinds
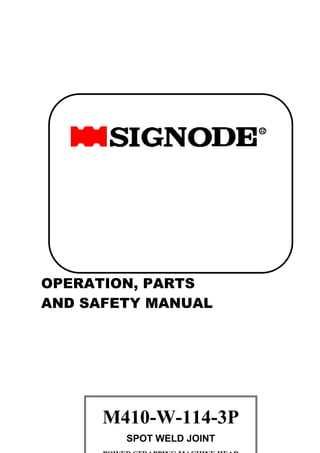
Addressing the functionality of key systems in woodwind instruments is essential for maintaining optimal performance. This section covers various aspects of enhancing these mechanisms, ensuring they operate smoothly and efficiently. Understanding the common issues and maintenance techniques can greatly improve the longevity and playability of these musical tools.
Common Issues with Key Mechanisms
- Sticky keys due to moisture or dirt accumulation
- Misalignment of keys causing operational difficulties
- Worn pads leading to air leaks
- Loose screws affecting stability
Maintenance and Troubleshooting Techniques
- Cleaning: Regularly clean the keys and surrounding areas with a soft cloth to remove moisture and debris.
- Alignment: Check the alignment of keys by gently pressing them and observing their movement. Adjust as necessary.
- Pad Replacement: Replace worn or damaged pads to ensure a proper seal and prevent air leaks.
- Screw Tightening: Inspect all screws for looseness and tighten them to maintain stability.
Fixing Valves and Pistons in Brass
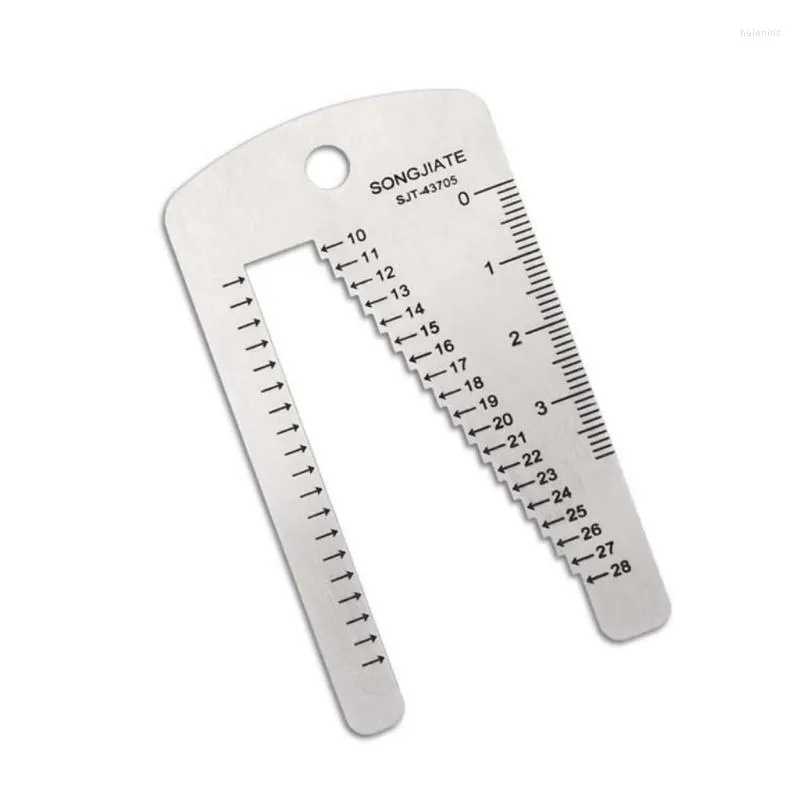
Maintaining the functionality of mechanical components is essential for ensuring optimal performance. Over time, these parts can encounter various issues, leading to decreased efficiency and sound quality. Understanding the common problems and solutions associated with these elements can help restore their proper function.
Common Issues: One of the most frequent challenges involves sticking valves or pistons, which can hinder movement and affect the overall sound production. Accumulated dirt, moisture, or corrosion often contribute to these issues. Regular cleaning and lubrication are crucial for preventing such problems.
Repair Process: To address sticking components, disassemble the affected parts carefully. Use a suitable cleaning solution to remove debris and corrosion. After cleaning, apply a thin layer of lubricant designed for brass. Reassemble the components, ensuring proper alignment for optimal movement.
Prevention Tips: Regular maintenance is vital for extending the lifespan of these parts. Cleaning after each use, storing the brass in a controlled environment, and periodic inspections can significantly reduce the likelihood of future issues.
Tuning and Adjusting String Instruments
Achieving the right pitch and tone is essential for the optimal performance of stringed musical devices. This section explores effective techniques to ensure these items are finely tuned and adjusted for accurate sound production.
Proper tuning involves aligning the pitches of the strings to a specific standard, while adjustments may address various factors affecting sound quality.
Basic Tuning Techniques
- Using a Tuner: Electronic tuners can provide precise pitch readings, making it easier to achieve the desired tone.
- Tuning Fork: This traditional method uses a vibrating metal fork to create a reference pitch.
- Relative Tuning: Musicians can match the pitches of strings against one another to ensure harmonious sounds.
Adjustment Factors
- String Height: Adjusting the action of the strings can enhance playability and sound clarity.
- Intonation: Ensuring that notes sound accurate across the fretboard is crucial for overall tuning.
- Bridge and Nut Positioning: The correct placement of these components affects both tuning stability and sound projection.
By employing these methods and making necessary adjustments, musicians can maintain the integrity and quality of their stringed musical devices.
Care Tips for Percussion Instruments
Maintaining the longevity and performance of your percussion gear is essential for achieving the best sound. Regular upkeep ensures that your gear remains in top condition and can withstand frequent use. Here are some practical recommendations to keep your percussion pieces in excellent shape.
- Regular Cleaning: Wipe down surfaces after each use to remove dirt, moisture, and oils. Use a soft cloth for delicate finishes.
- Proper Storage: Store your gear in a cool, dry place. Avoid direct sunlight and extreme temperatures that can warp or damage components.
- Check for Damage: Regularly inspect your pieces for any signs of wear or damage. Address issues promptly to prevent further deterioration.
- Use Quality Accessories: Choose high-quality mallets, heads, and stands to enhance performance and reduce wear on your gear.
- Tuning and Adjustments: Ensure that all components are correctly tuned and adjusted for optimal sound quality.
By following these tips, you can help preserve the functionality and aesthetic of your percussion gear, ensuring it sounds its best for years to come.
Preventing Moisture Damage in Instruments
Protecting musical devices from humidity is crucial for maintaining their performance and longevity. Excessive moisture can lead to deterioration, causing functional issues and affecting sound quality. Implementing effective strategies to minimize exposure to damp conditions ensures that these precious tools remain in optimal working condition.
Storage Solutions
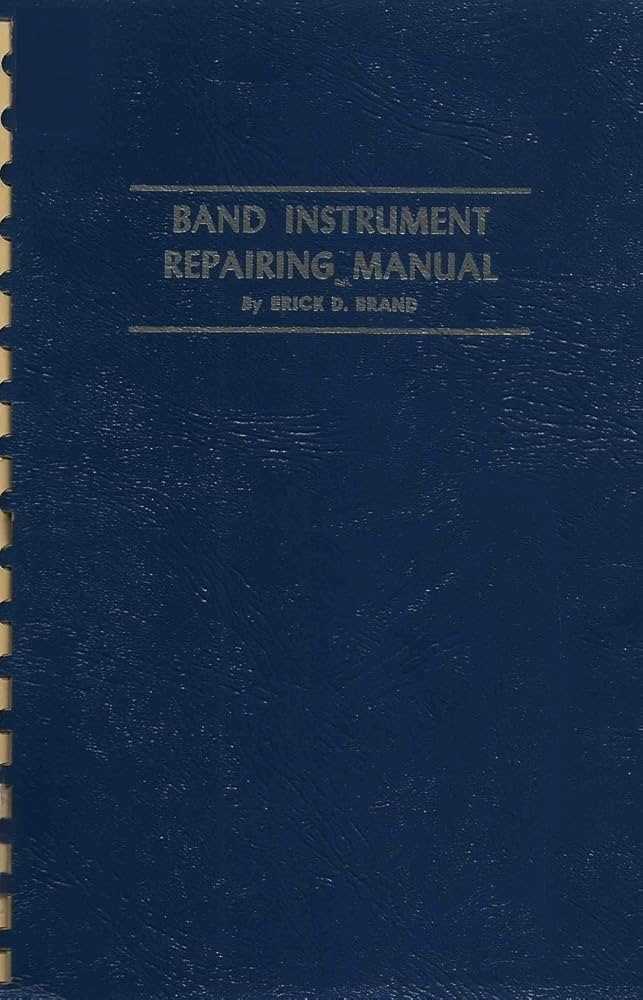
One of the most effective ways to prevent moisture damage is through proper storage. Keep instruments in a controlled environment, ideally at room temperature with low humidity levels. Using cases with moisture-absorbing materials can significantly reduce humidity inside. Regularly check the condition of storage areas and make necessary adjustments to maintain a dry atmosphere.
Regular Maintenance Practices
Consistent upkeep is vital for preventing moisture-related issues. Wipe down surfaces after each use to remove any accumulated moisture. Additionally, consider using desiccant packs inside cases to absorb excess humidity. By integrating these practices into your routine, you can significantly extend the lifespan and functionality of your musical devices.
Replacing Pads, Springs, and Corks
Over time, certain components within a musical device may wear out, affecting its performance and sound quality. This section outlines the essential procedures for updating key parts that contribute to the functionality and resonance of the device. Proper maintenance ensures optimal playability and enhances the overall experience for the musician.
Identifying Worn Components
Before beginning the replacement process, it’s crucial to inspect the various elements carefully. Look for signs of wear such as cracks, discoloration, or a lack of elasticity in springs. Pads may feel uneven or compressed, while corks can become brittle or discolored. Identifying these issues early can prevent further damage and ensure a smoother replacement process.
Replacement Process
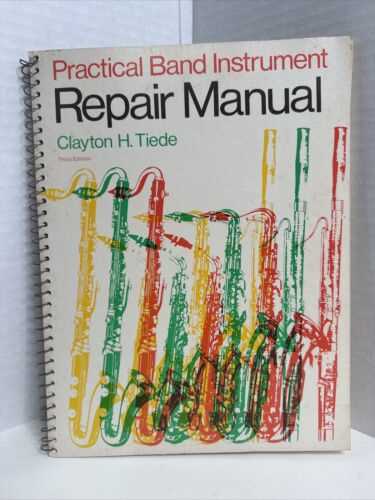
To replace worn components, gather the necessary tools, including a pad puller, spring hook, and appropriate replacement parts. Carefully remove the old pads using the pad puller, taking care not to damage the surrounding areas. Next, use the spring hook to detach and replace any springs that have lost their tension. Finally, replace corks by removing the old ones and applying new ones securely. Ensure everything is aligned correctly to maintain the instrument’s integrity and functionality.