Understanding and identifying frequent issues in this utility vehicle can help operators maintain smooth functionality and prolong its usage. This section covers common operational challenges, offers potential solutions, and highlights areas requiring periodic checks.
Issue |
Possible Cause |
Solution |
Engine Not Starting |
Weak battery, clogged fuel filter |
Check battery charge, replace or clean fuel filter |
Hydraulic System Slow |
Low hydraulic fluid, clogged lines |
Refill hydraulic fluid, inspect and clear lines |
Hydraulic System Inspection and Repairs
Ensuring optimal functionality of the hydraulic components is essential for efficient operation. Regular examination of these systems helps in identifying wear and potential issues before they escalate. In this section, we outline the steps for a thorough inspection, aiming to maintain smooth and responsive performance.
Visual Inspection: Begin by examining the system for any visible signs of wear, such as leaks, cracked hoses, or corroded connections. Confirm that each line and fitting is securely connected and free of damage. Identifying these signs early can prevent more significant malfunctions.
Fluid Check: Maintaining adequate hydraulic fluid levels is crucial for seamless operation. Low fluid levels can cause irregular movements or power loss. Regularly check fluid levels, and ensure the fluid is clean and uncontaminated. Refill or replace fluid as needed to prevent unnecessary strain on the system.
Pressure Testing: Utilizing pressure gauges, check the system’s pressure levels to ensure they are within recommended ranges. Variations in pressure may indicate blockages or pump issues, which can hinder overall efficiency. Perform tests under standard working conditions to assess performance accurately.
Component Maintenance: Periodically clean and lubricate essen
Engine Diagnostics and Performance Tips
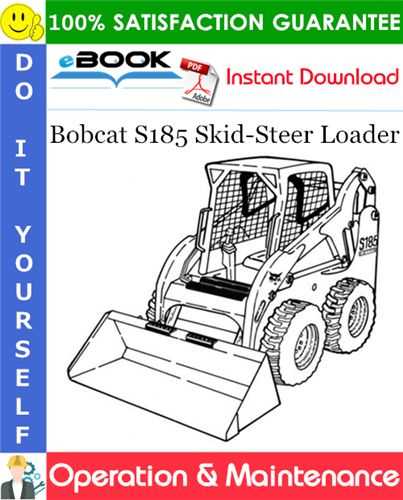
Ensuring optimal functioning of a mechanical power unit is crucial for efficiency and longevity. Regular assessments and maintenance can help identify issues early, preventing extensive damage and costly repairs. Here are key considerations for enhancing engine diagnostics and performance.
Essential Diagnostic Steps
- Visual Inspection: Regularly check for leaks, worn belts, and loose connections.
- Fluid Levels: Maintain appropriate levels of oil, coolant, and fuel.
- Error Codes: Utilize diagnostic tools to read any fault codes from the control system.
- Air Filter Condition: Inspect and replace air filters as needed to ensure proper airflow.
Performance Enhancement Tips
- Fuel Quality: Use high-quality fuel to improve combustion efficiency.
- Regular Maintenance: Follow a consistent maintenance schedule to keep all components in top shape.
- Proper Load Management: Avoid overloading the unit to prevent strain on the engine.
- Temperature Monitoring: Keep an eye on operating temperatures to avoid overheating.
By following these guidelines, operators can ensure that their mechanical units operate efficiently and effectively, leading to improved performance and reduced downtime.
Electrical System Maintenance Essentials
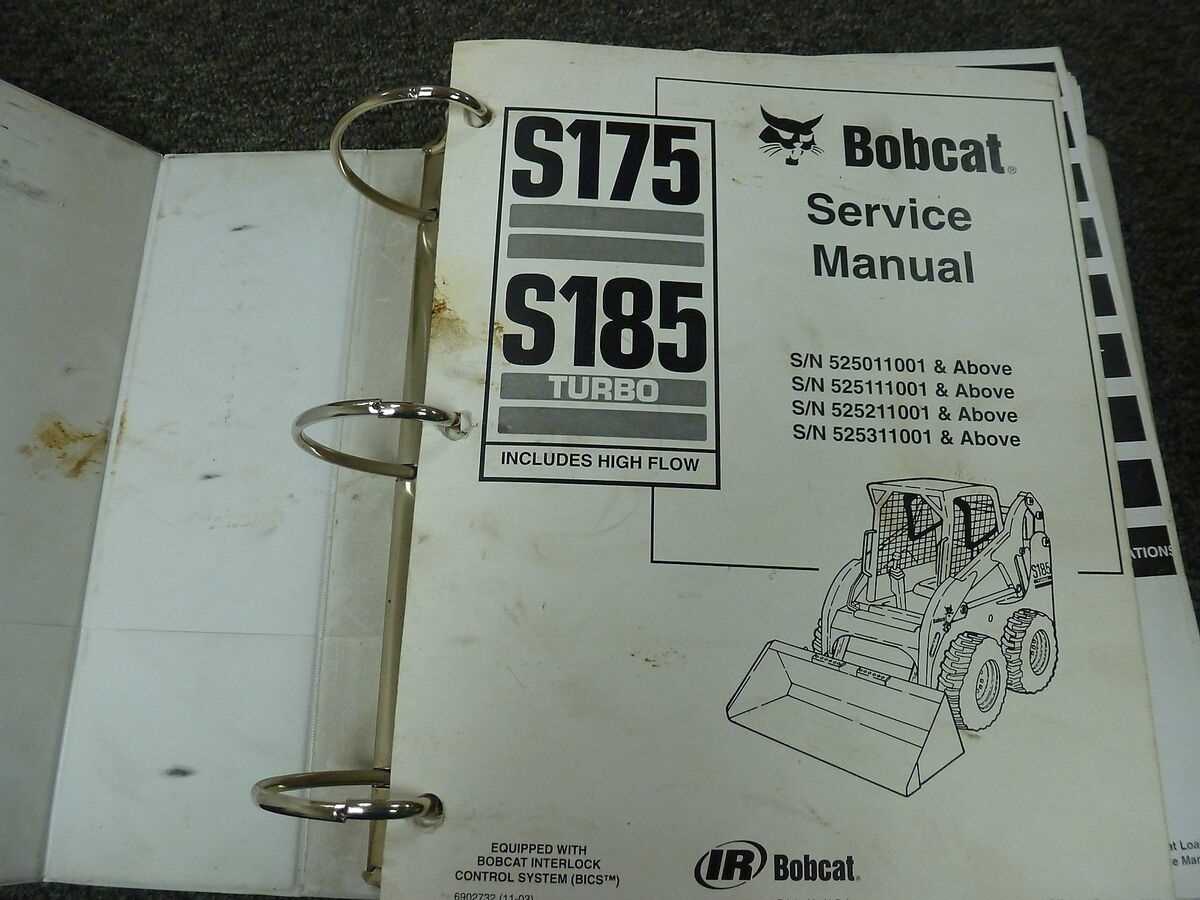
Maintaining the electrical components of machinery is crucial for ensuring optimal performance and longevity. Regular inspections and upkeep help identify potential issues before they escalate, leading to more significant problems and costly repairs.
To effectively manage the electrical system, consider the following key practices:
- Regular Inspections: Schedule frequent evaluations of wiring, connections, and components to detect any signs of wear or damage.
- Cleaning Connections: Ensure all electrical terminals are clean and free from corrosion to maintain efficient conductivity.
- Battery Maintenance: Check battery levels and terminals regularly to ensure they are secure and functioning properly.
- Testing Circuitry: Utilize diagnostic tools to test circuits and identify any irregularities in voltage or resistance.
By adhering to these fundamental practices, operators can significantly enhance the reliability and efficiency of their equipment’s electrical systems.
Replacing and Adjusting S185 Components
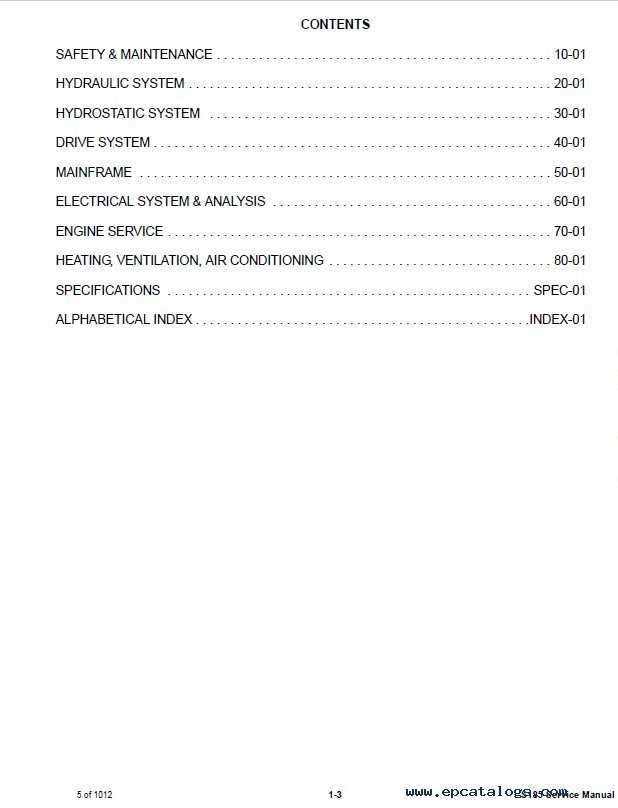
Maintaining optimal performance in heavy machinery involves the careful replacement and adjustment of various parts. This section outlines essential practices to ensure that components are functioning correctly, enhancing overall efficiency and longevity.
Key considerations when undertaking replacements include:
- Identifying the specific components that require attention.
- Utilizing appropriate tools and safety gear to prevent accidents.
- Following manufacturer guidelines to ensure compatibility and reliability.
For effective adjustment, follow these steps:
- Consult the specifications for the component in question.
- Make necessary adjustments to achieve the correct settings.
- Test the machinery post-adjustment to verify improvements.
Regular monitoring and timely replacements can significantly reduce downtime and enhance performance, contributing to smoother operations in the field.
Maintenance Schedule for Optimal Performance
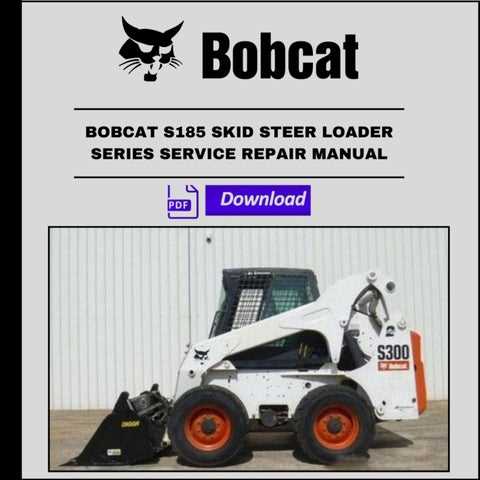
Regular upkeep is essential for ensuring the longevity and efficiency of any machinery. Adhering to a well-structured maintenance timetable helps in identifying potential issues before they escalate, thereby enhancing overall functionality. This proactive approach not only minimizes downtime but also contributes to better performance and reliability over time.
Daily Maintenance Checks
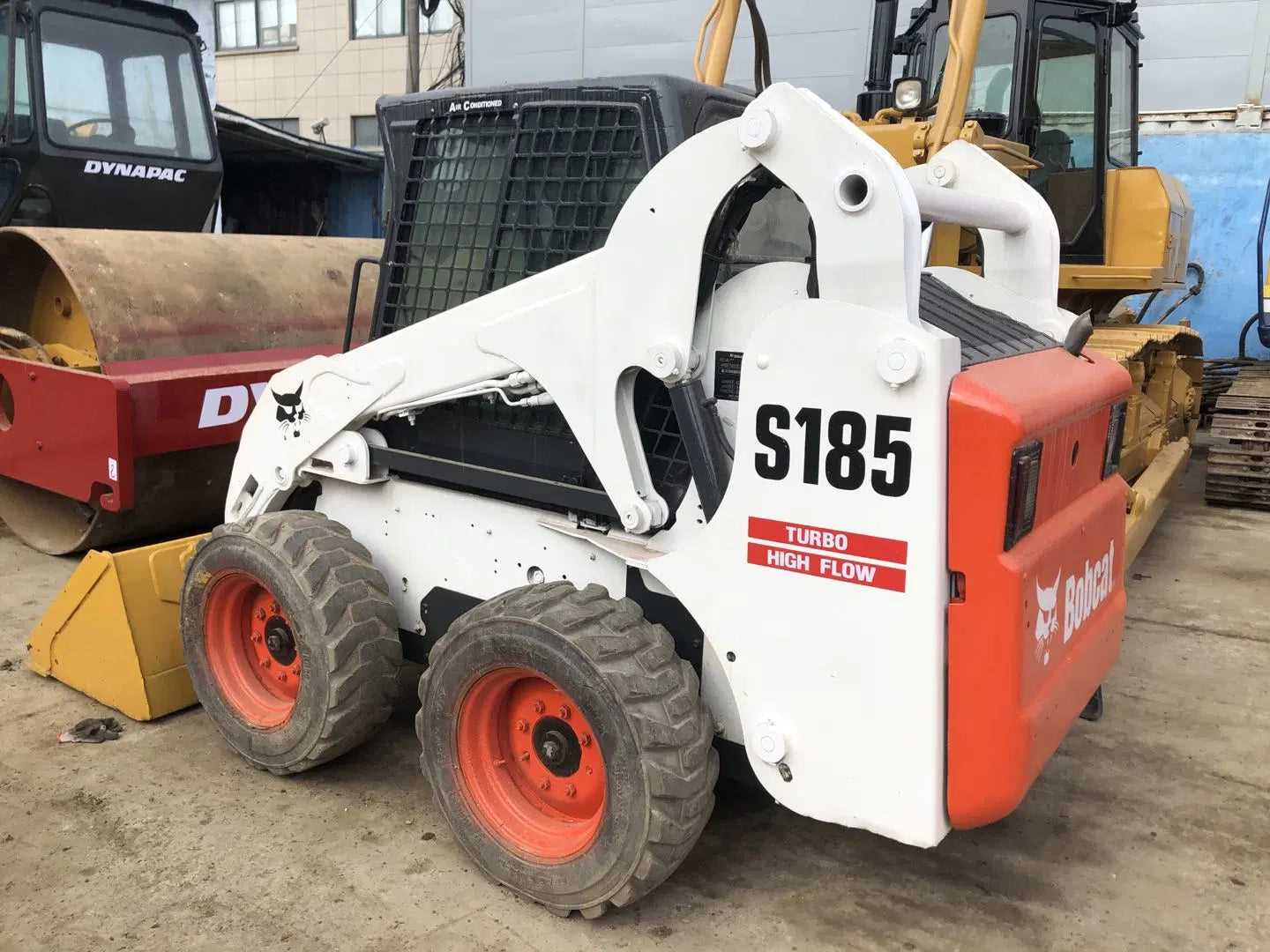
Before each use, a series of quick inspections should be conducted. This includes checking fluid levels, inspecting for leaks, and ensuring that all safety features are operational. Regular monitoring of these elements can prevent minor problems from becoming significant repairs.
Weekly and Monthly Procedures
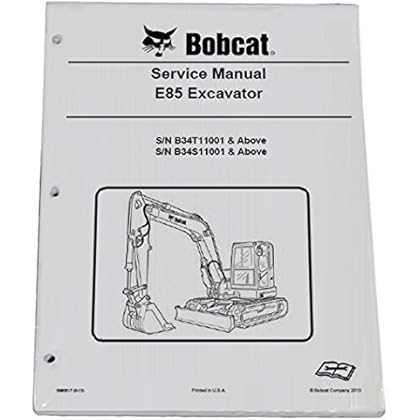
In addition to daily checks, weekly tasks should involve cleaning air filters and examining the hydraulic system for any signs of wear. Monthly maintenance should include a comprehensive inspection of the undercarriage and track systems, along with replacing worn components. Following these intervals ensures that the machinery remains in peak condition and ready for operation.
Safety Practices During S185 Repairs
When engaging in maintenance tasks on heavy machinery, ensuring safety is paramount. Adhering to established guidelines helps to prevent accidents and injuries, creating a secure environment for all personnel involved. This section outlines essential precautions that should be taken to foster a safe working atmosphere while conducting servicing activities.
Essential Safety Equipment
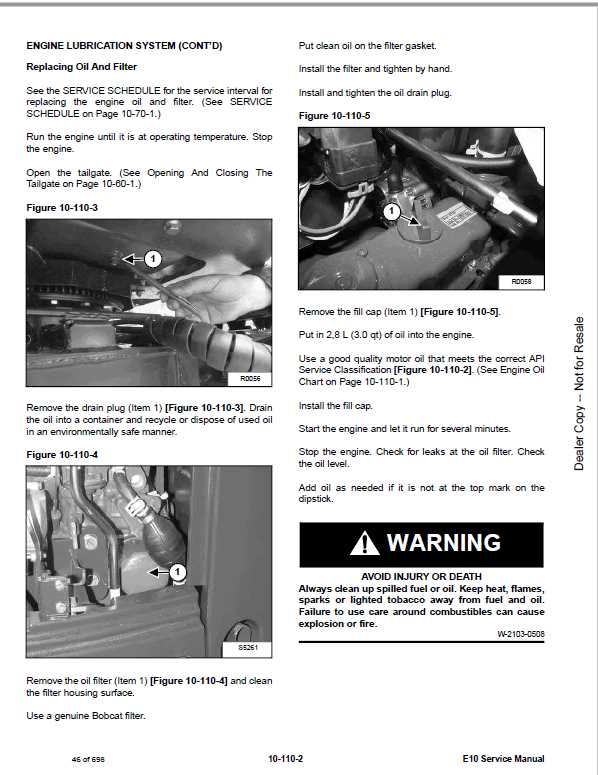
Utilizing appropriate safety gear is crucial for minimizing risks. The following items should always be worn during servicing:
- Hard hats to protect against falling objects
- Safety glasses to shield eyes from debris
- Gloves designed for mechanical work
- Steel-toed boots to safeguard feet from heavy equipment
- High-visibility vests for better visibility on job sites
Safe Working Environment
Creating a secure workspace is vital for effective servicing. Consider these practices:
- Maintain a clean area to prevent slips and trips
- Ensure proper ventilation when working with chemicals
- Keep emergency equipment accessible and in good condition
- Utilize barriers or cones to designate work zones
- Conduct regular safety inspections of tools and machinery
Tips for Extending Bobcat S185 Lifespan
Maintaining the longevity of heavy machinery is crucial for optimal performance and cost-effectiveness. Implementing proper care and regular checks can significantly enhance the durability and reliability of your equipment. Here are some essential strategies to consider.
1. Regular Maintenance Checks: Schedule consistent inspections to identify potential issues before they escalate. This proactive approach allows for timely interventions, ensuring that all components function smoothly.
2. Lubrication: Ensure all moving parts are adequately lubricated. Proper lubrication minimizes friction, reducing wear and tear, which is vital for extending the operational life of the machinery.
3. Clean Air Filters: Regularly clean or replace air filters to ensure the engine breathes effectively. Clogged filters can lead to decreased performance and increased fuel consumption.
4. Monitor Operating Conditions: Be mindful of the working environment. Avoid excessive load conditions and operate within the machine’s specified limits to prevent undue stress on components.
5. Proper Storage: When not in use, store your equipment in a clean, dry place. Protecting it from harsh weather conditions and contaminants can prevent rust and deterioration.
By adhering to these best practices, you can significantly increase the lifespan of your heavy machinery, ensuring efficient operation and reducing long-term costs.